Über Zieta
MEHR üBER ZIETA
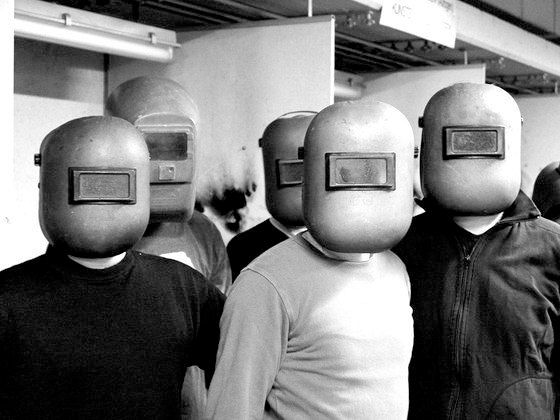
Zieta Prozessdesign, derzeit als Zieta Studio tätig, wurde 2010 von Oskar Zieta gegründet - einem Architekten und Innovator, dem CEO der Marke. Es ist ein interdisziplinäres Team von Architekten, Designern, Ingenieuren und Technologen.
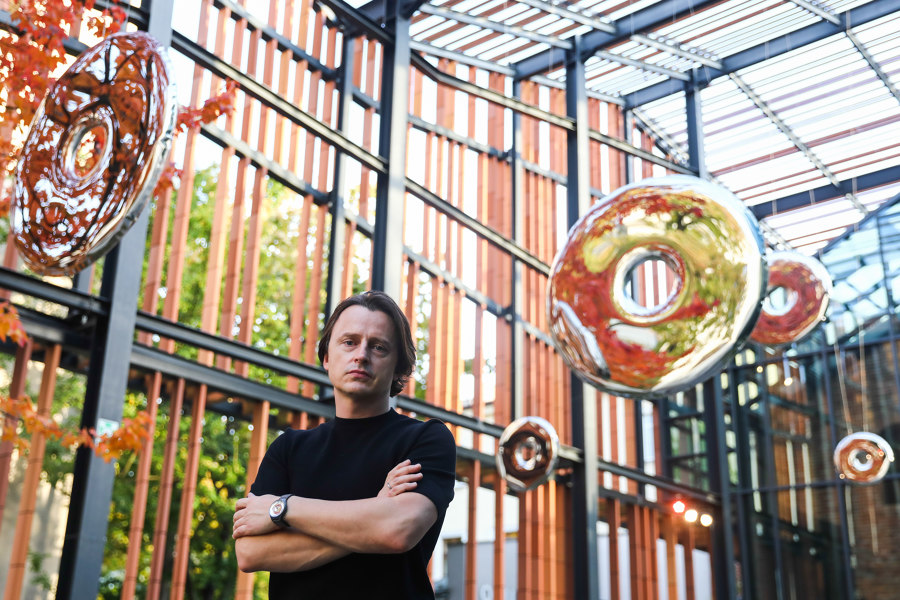
Als Prozessdesigner streben sie nicht nur danach, fabelhafte Formen zu entwerfen, sondern sie wollen innovative Lösungen schaffen, die endlose Möglichkeiten für Entwicklung und Nutzung schaffen. Zieta Studio entwirft Prozesse, die inspirieren und zu unvorhersehbaren Ergebnissen und Formen führen.
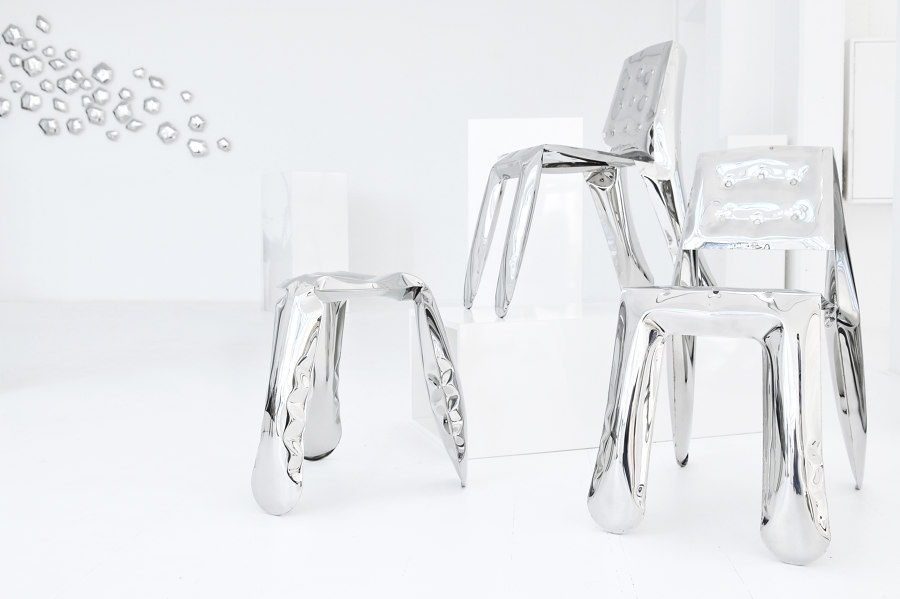
Das Studio verwendet einen computergesteuerten Produktionsprozess, der es ihm ermöglicht, ein individuelles Muster, eine kundenspezifische Form sowie eine kundenspezifische Funktion zu liefern - ein einzigartiges Produkt, das mit viel Liebe zum Detail hergestellt wird. Durch das Experimentieren mit Formen und Gestalten schafft Zieta Studio für Menschen, die die Designentwicklung als einen wichtigen Faktor im Produktionsprozess betrachten.
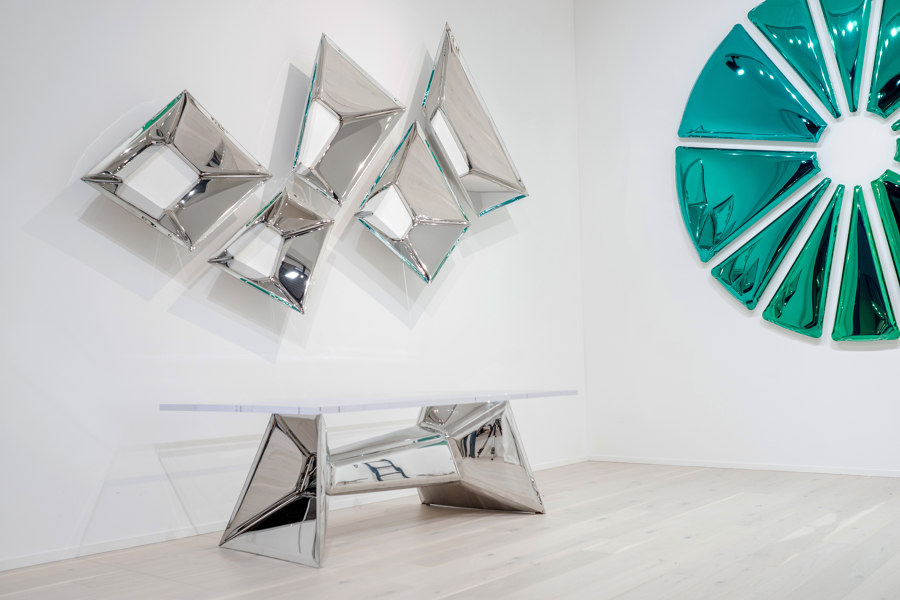
Die Philosophie von Zieta spiegelt sich in den von ihnen hergestellten Produkten wider. Die FiDU-Technologie, mit der das Studio seine Sammlungen von Hockern, Stühlen, Spiegeln, Tischen und Accessoires herstellt, ist eine innovative Methode, um Bits in Atome umzuwandeln. Die heutige Welt ist überfüllt mit unnötigen und aufdringlichen Daten, daher legt Zieta Wert auf seine Produktionsprozesse, um nicht nur weniger Material, sondern auch weniger Daten zu verwenden.
Wirkung dieser Forschung findet sich in den Sammlungen von Objekten, die am Rande von Ästhetik und Funktion entstanden sind, Möbeln und dekorativen Wohnskulpturen, die die Eigenschaften von Stahl neu definieren und das transformative Potenzial der Technologie zeigen:
- Zieta Collection (2010)
- The Copper Collection
- The Heat Collection (2018)
- Out of Ordinary (2018)
- The Gradient Collection (2019)
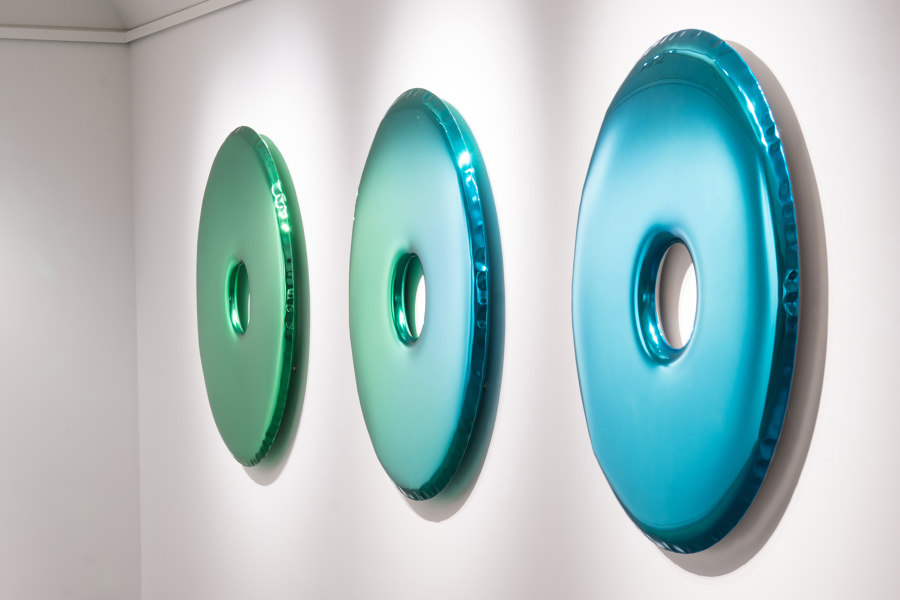
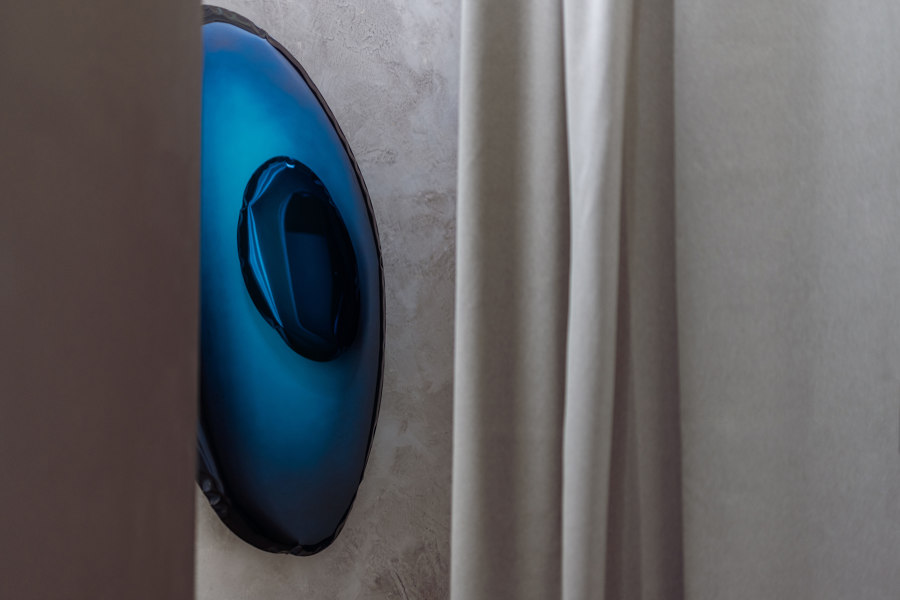
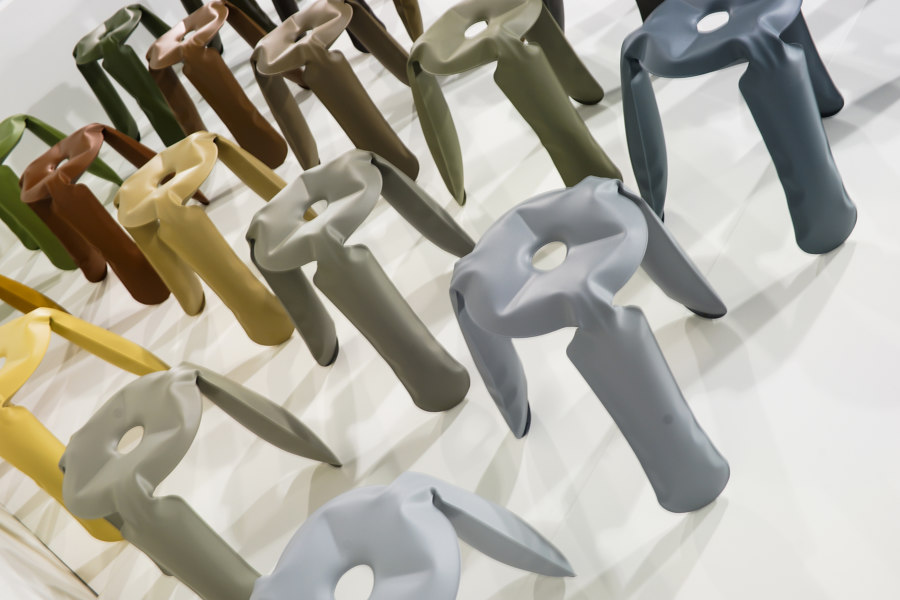
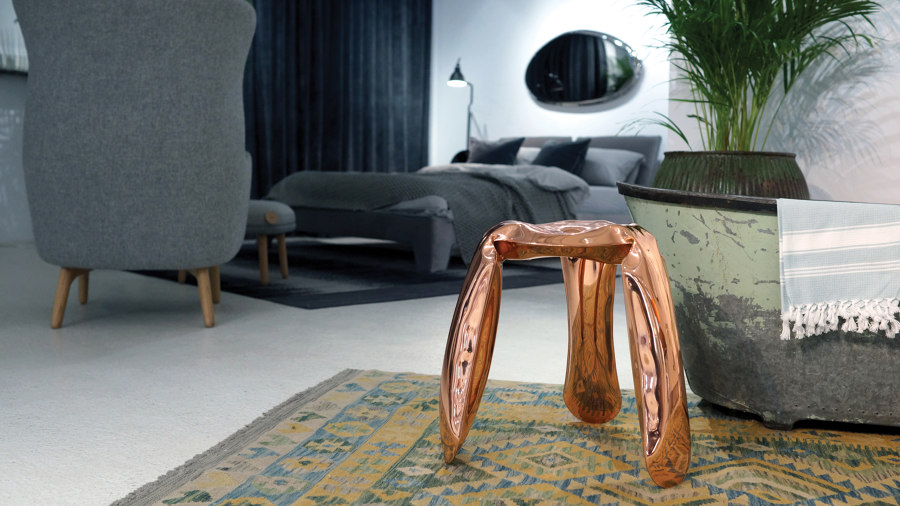
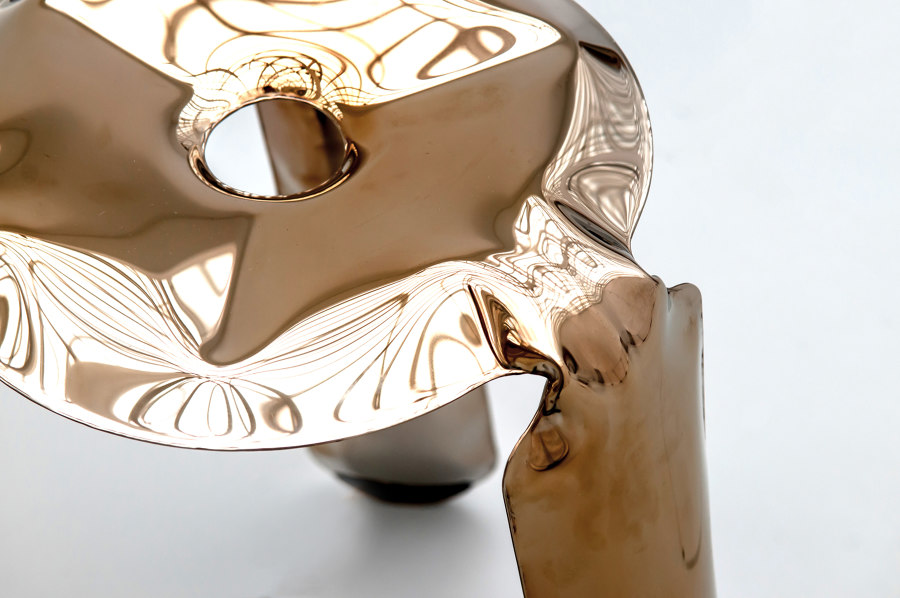
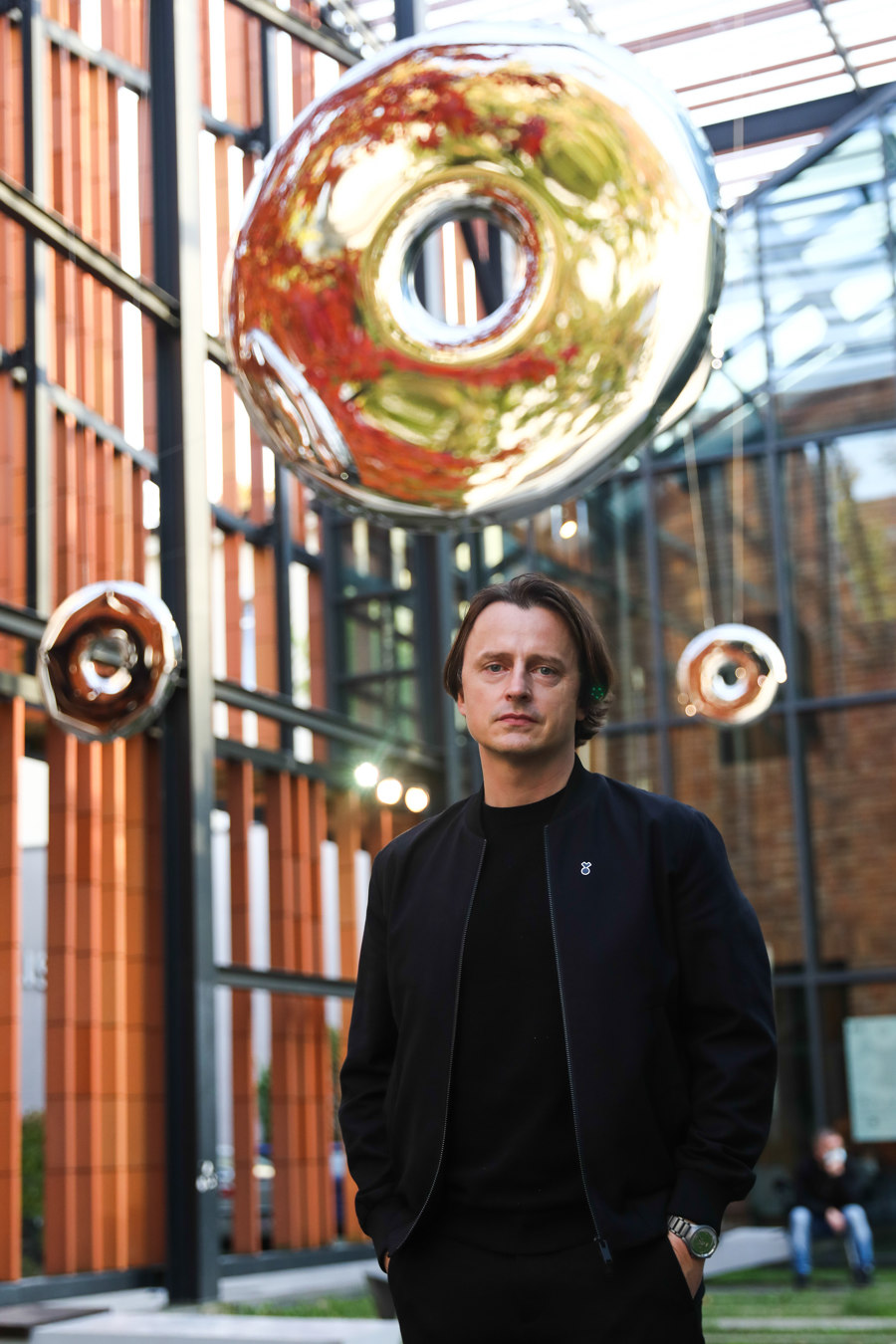
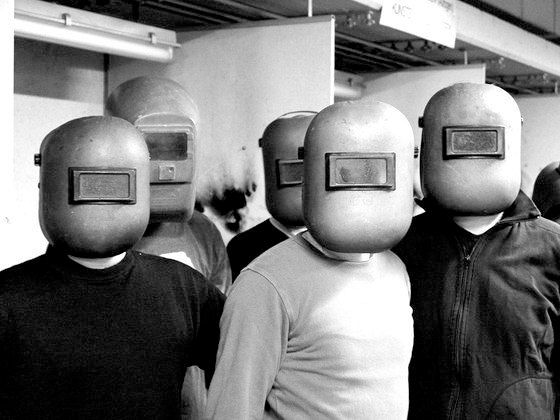
Zieta Prozessdesign, derzeit als Zieta Studio tätig, wurde 2010 von Oskar Zieta gegründet - einem Architekten und Innovator, dem CEO der Marke. Es ist ein interdisziplinäres Team von Architekten, Designern, Ingenieuren und Technologen.
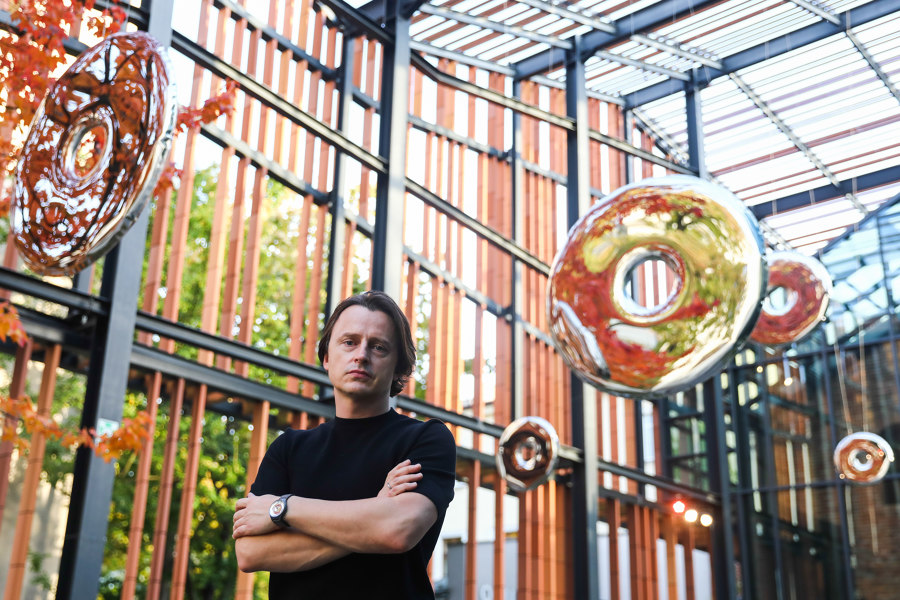
Als Prozessdesigner streben sie nicht nur danach, fabelhafte Formen zu entwerfen, sondern sie wollen innovative Lösungen schaffen, die endlose Möglichkeiten für Entwicklung und Nutzung schaffen. Zieta Studio entwirft Prozesse, die inspirieren und zu unvorhersehbaren Ergebnissen und Formen führen.
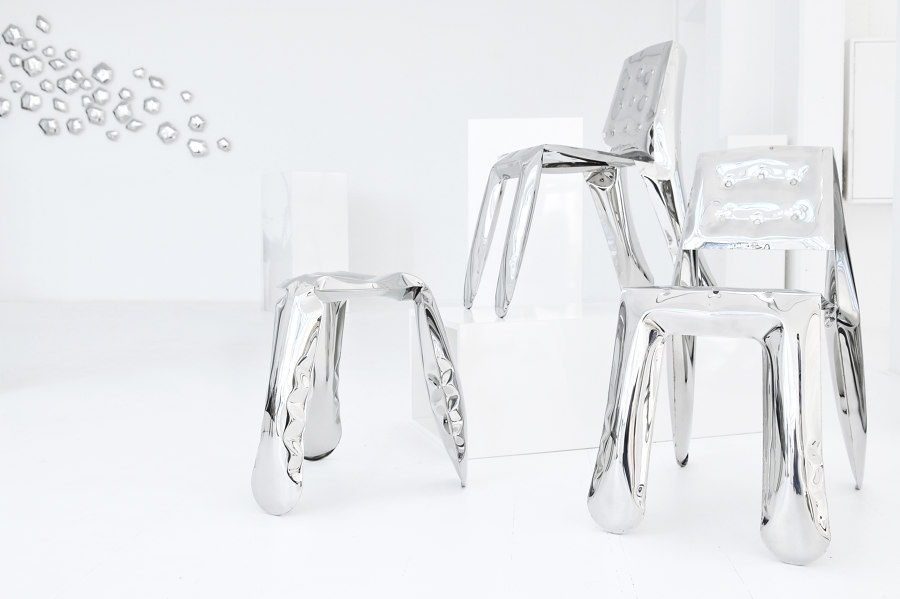
Das Studio verwendet einen computergesteuerten Produktionsprozess, der es ihm ermöglicht, ein individuelles Muster, eine kundenspezifische Form sowie eine kundenspezifische Funktion zu liefern - ein einzigartiges Produkt, das mit viel Liebe zum Detail hergestellt wird. Durch das Experimentieren mit Formen und Gestalten schafft Zieta Studio für Menschen, die die Designentwicklung als einen wichtigen Faktor im Produktionsprozess betrachten.
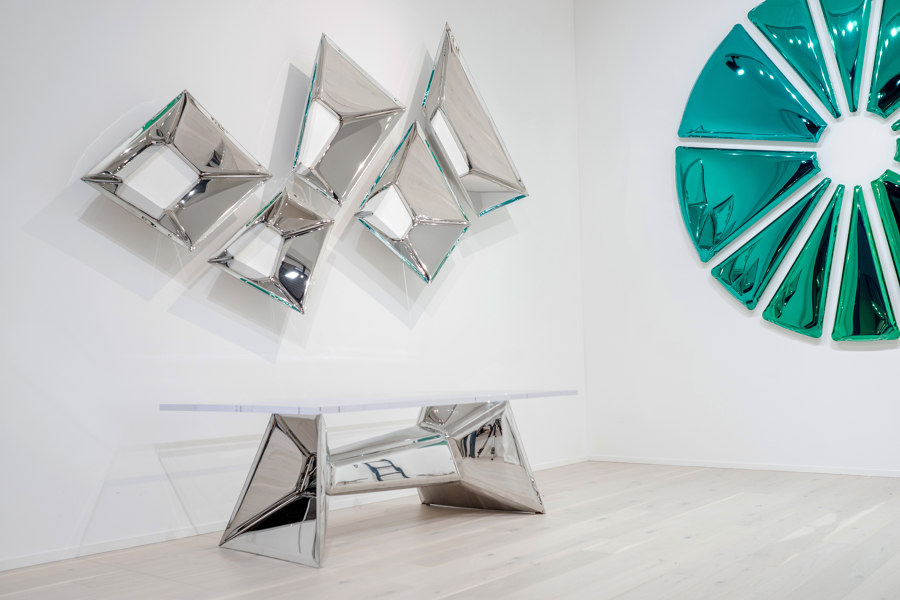
Die Philosophie von Zieta spiegelt sich in den von ihnen hergestellten Produkten wider. Die FiDU-Technologie, mit der das Studio seine Sammlungen von Hockern, Stühlen, Spiegeln, Tischen und Accessoires herstellt, ist eine innovative Methode, um Bits in Atome umzuwandeln. Die heutige Welt ist überfüllt mit unnötigen und aufdringlichen Daten, daher legt Zieta Wert auf seine Produktionsprozesse, um nicht nur weniger Material, sondern auch weniger Daten zu verwenden.
Wirkung dieser Forschung findet sich in den Sammlungen von Objekten, die am Rande von Ästhetik und Funktion entstanden sind, Möbeln und dekorativen Wohnskulpturen, die die Eigenschaften von Stahl neu definieren und das transformative Potenzial der Technologie zeigen:
- Zieta Collection (2010)
- The Copper Collection
- The Heat Collection (2018)
- Out of Ordinary (2018)
- The Gradient Collection (2019)
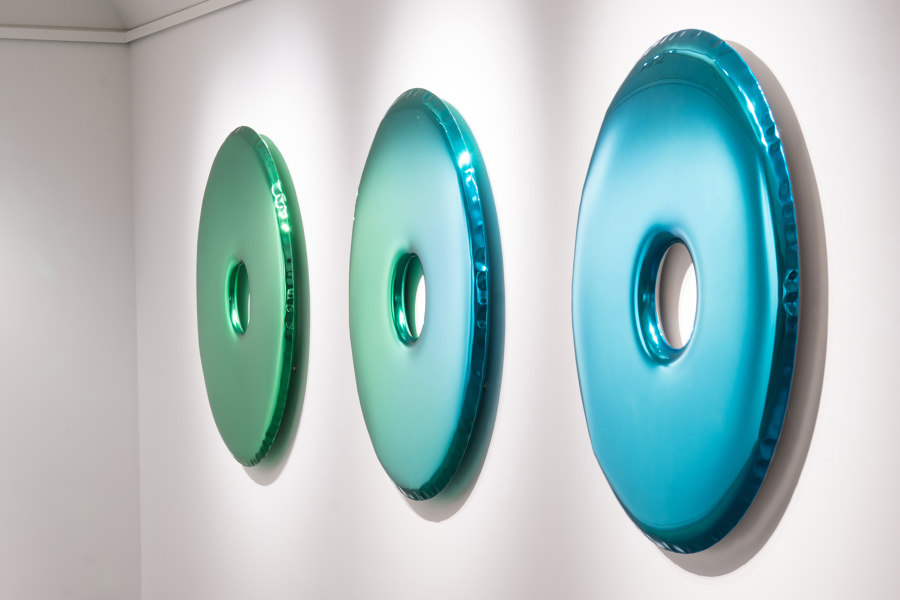
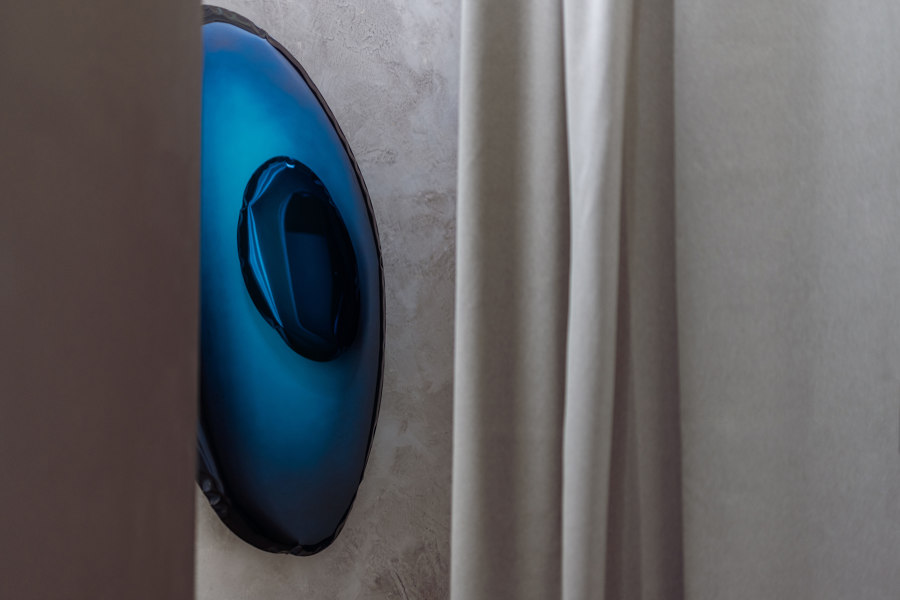
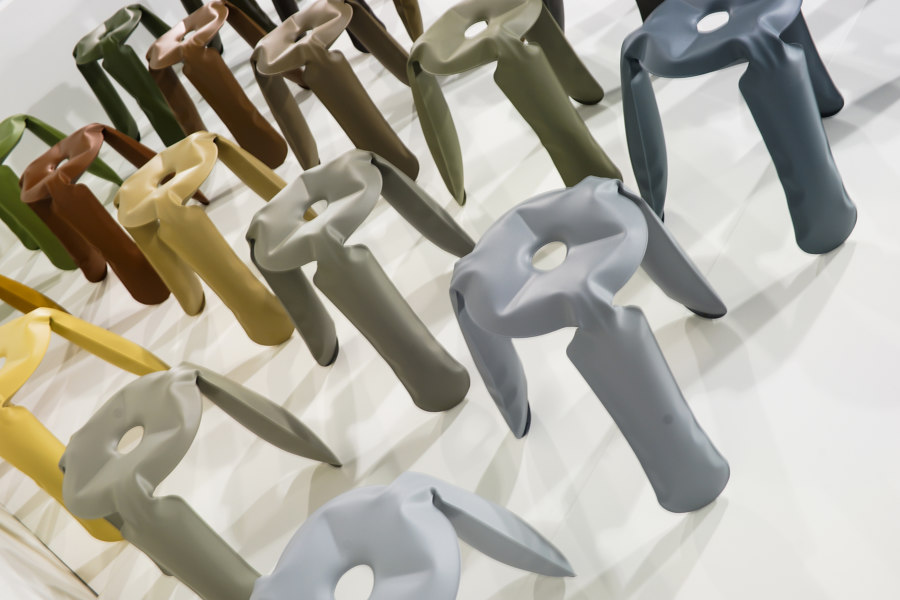
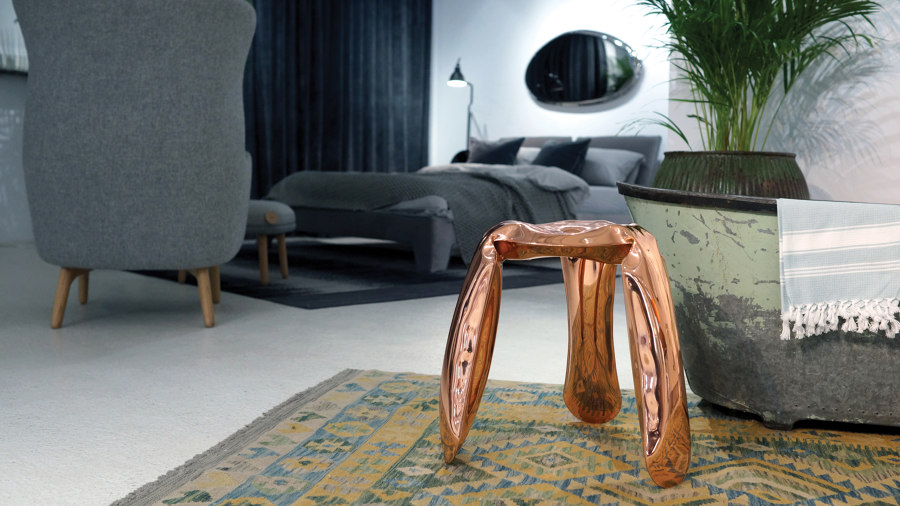
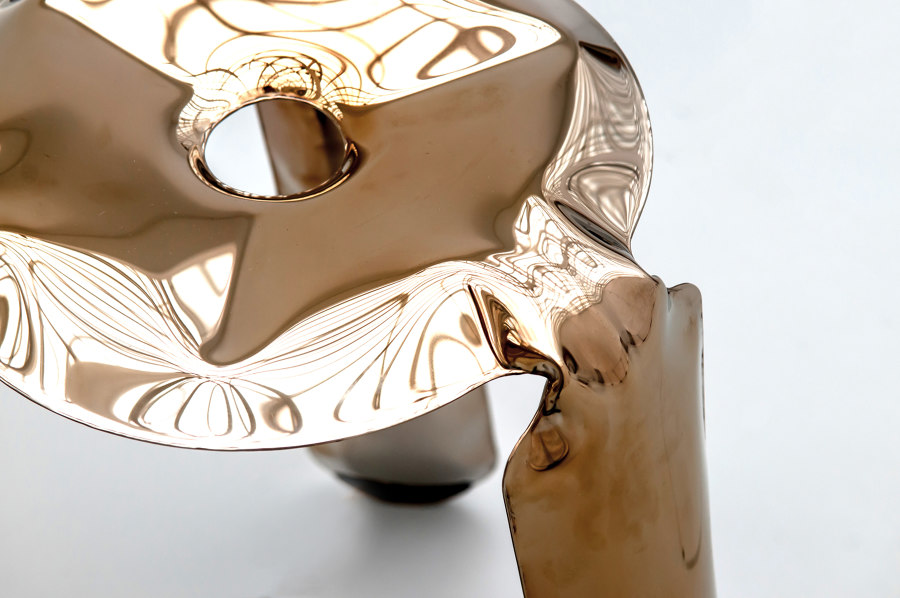
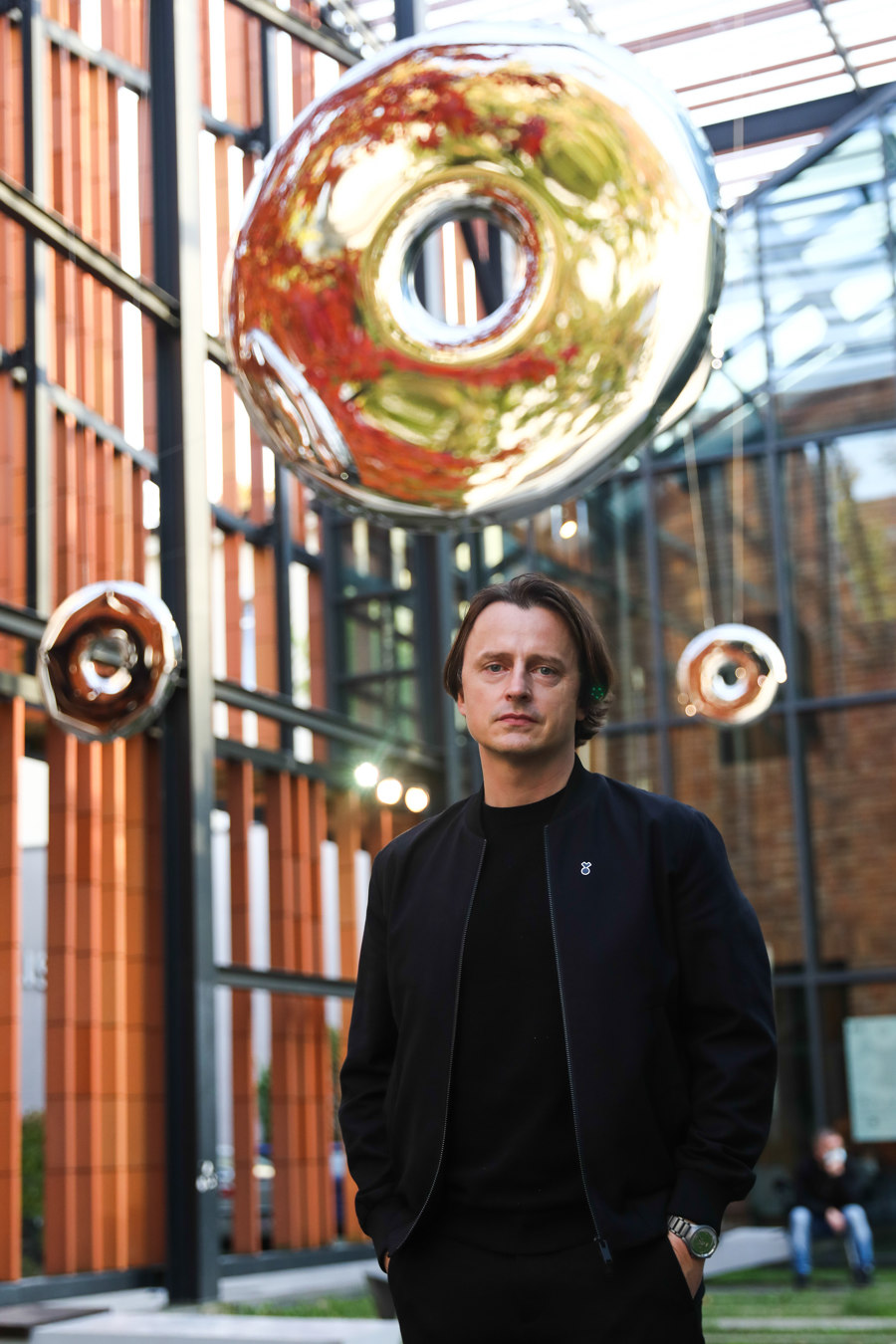
MEHR üBER ZIETA