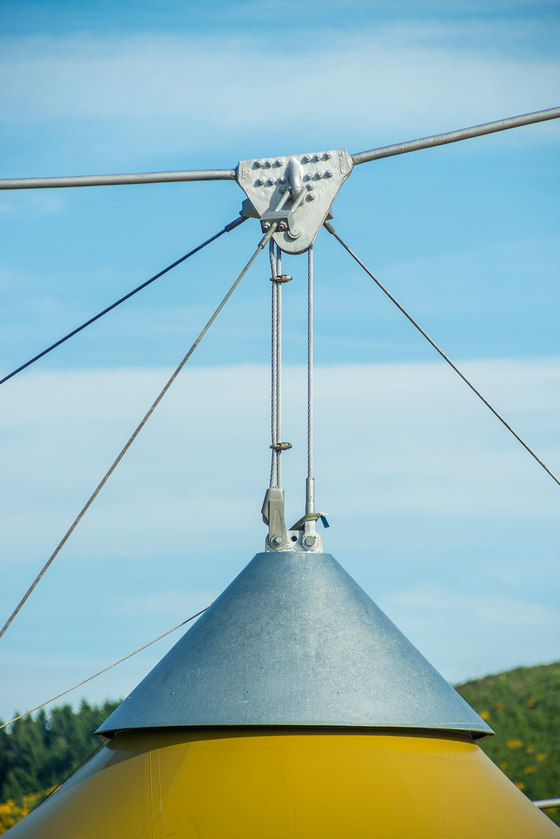
Fotógrafo: Guido Michallik
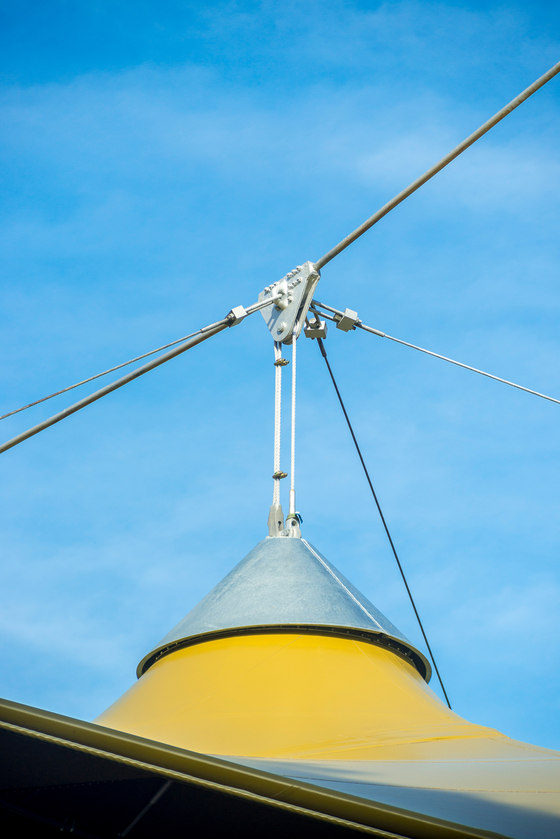
Fotógrafo: Guido Michallik
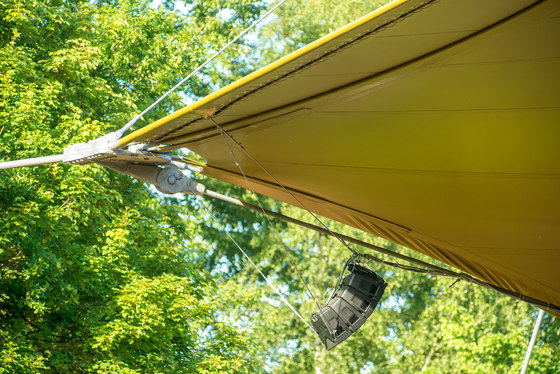
Fotógrafo: Guido Michallik
Since 1978 the 4,400 spectators in front of the outdoor stage of the Karl May Festival in Elspe in Sauerland have had a dry place to sit. With a roofed over base area of approx. 2,200 m² the roofing, which can be seen from a great distance, was one of the largest winter-proof lightweight suspended structures in Europe, behind the roof of the Munich Olympia Stadium. The stage got its new membrane roof in good time for the 2015 festival.
Analysis of the statics
To meet today's requirements imposed on textile architecture, prior to the dismantling a detailed 3D on-site measurement of the existing structure was prepared. Using this on-site measurement, the former statics, at the time mostly prepared by hand-written calculations were analyzed by the engineering firm, Büro Teschner Ingenieure. In this process it turned out that the hand-written calculations were astonishingly close to the computer-assisted calculation results. In 1978 the pre-cuts for the manufacturing of the roof membrane were still taken from a model (scale 1:33.3). Today the shape of the roof is determined with computer support and the precut files are generated by complex mathematical models.
Development of a new membrane
As was the case 37 years ago, the company Mehler Texnologies, one of the oldest membrane manufacturers in Europe, delivered the high-strength PVC-coated polyester fabric. In spite of the tight schedule, a new membrane was developed especially for the Elspe Festival. Based on the old roof, the roof membrane was to be manufactured in a special green tone. After running through the required certifications there was no reason not to use the 1.3 mm thin fabric, approx. 1.5 kg/m² in weight. The high strength design enables a break resistance of approx. 18 to/m.
Assembly
For the assembly of the roof, at the company Koch Membranen from Rimsting, Germany with more than 45 years of experience in membrane construction, a total of 4,600 m² membrane material was required to manufacture the roof surface with over 2,600 m² from this material. The fabric, delivered on large rolls with a width of 2.5 m, was first cut to size in 270 individual sections on automatic cutting machines, then it was processed with modern high-frequency welding technology and heavy-duty sewing machines in three partial surfaces of to 900 m². Areas of the roof that are subject to particularly high load, e.g. the 9 high-points, are assembled with two membrane layers and thus withstand incredible loads of up to 36 to/m.
Installation
For membrane structures in this order of magnitude, in addition to the precise preliminary manufacturing in the plant, a conscientious pre-planning of the installation sequences is also required. In spite of the adverse weather it was possible to install the roof faster than planned. For the installation, initially the three partial surfaces were pre-assembled on the ground to the extent possible, in order to then be lifted into the air as a complete unit. After all threaded fittings and sealing connections on the membrane butts and edges were completed, the roof membrane was pulled up to its final position. For the last step the high-point covers of galvanized sheet steel were mounted. They gave the roof its final touch.
engineering: teschner ingenieure
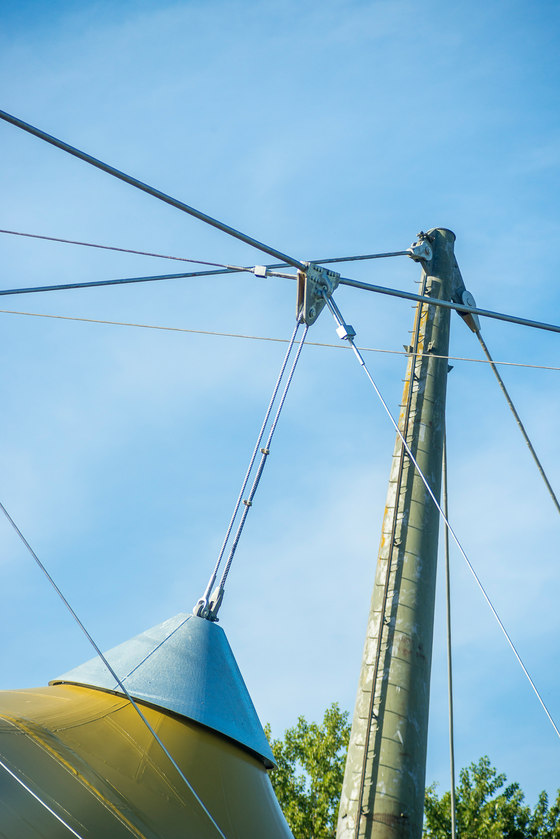
Fotógrafo: Guido Michallik
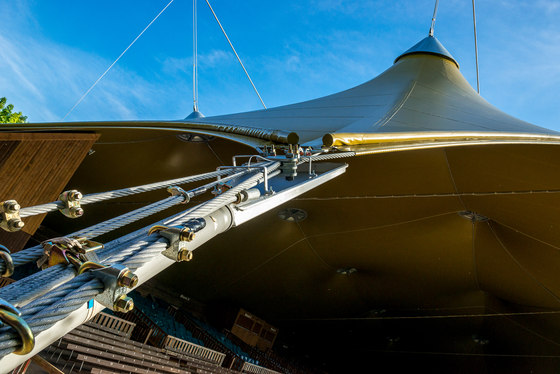
Fotógrafo: Guido Michallik
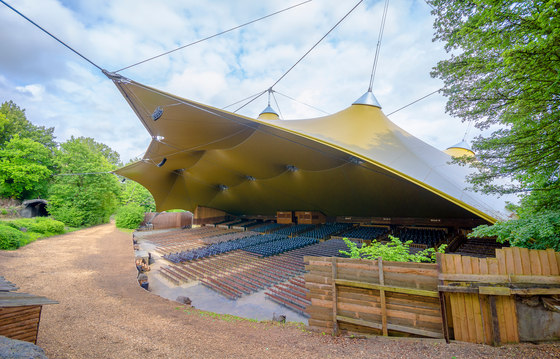
Fotógrafo: Guido Michallik
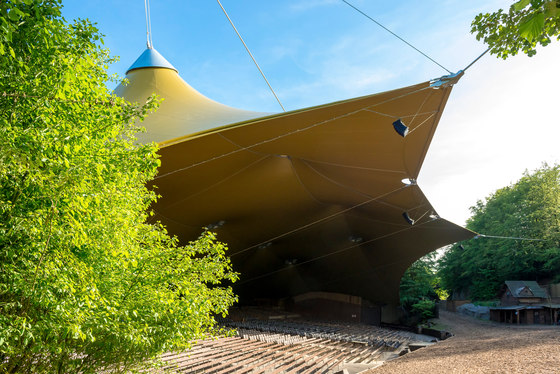
Fotógrafo: Guido Michallik
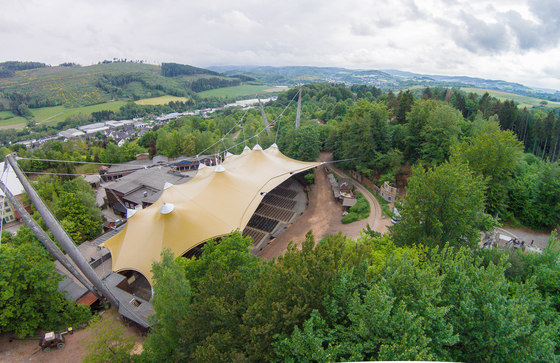
Fotógrafo: Guido Michallik
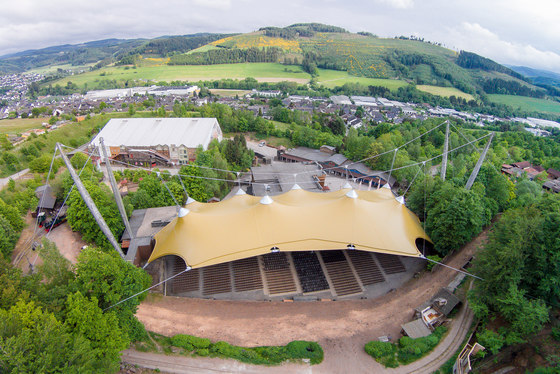
Fotógrafo: Guido Michallik
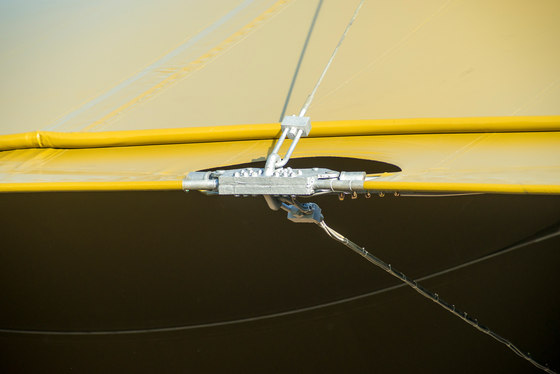
Fotógrafo: Guido Michallik
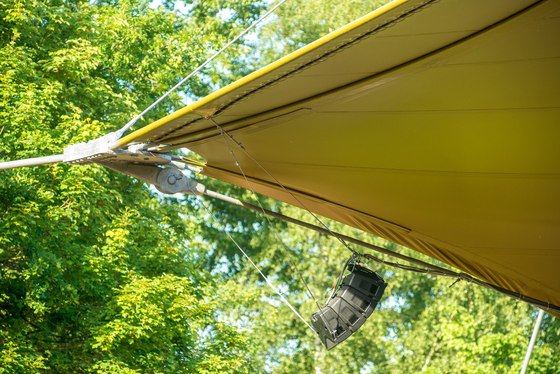
Fotógrafo: Guido Michallik
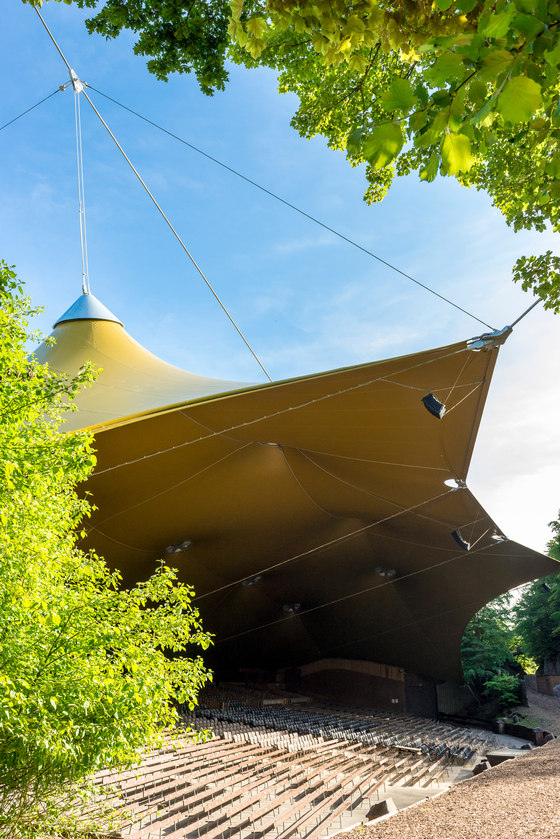
Fotógrafo: Guido Michallik