Japan Stories: Chiyozuru Sadahide
Text von 25portraits
Berlin, Deutschland
17.07.17
In the fourth installment of Japan Stories, Japanese bladesmith Chiyozuru Sadahide II and his apprentice Naohide challenge traditional techniques to create works that express the inherent beauty of iron and steel.
Chiyozuru Naohide (left) and Chiyozuru Sadahide II (right) in their workshop
Miki, in Hyogo prefecture, is well-known for being one of Japan’s most prominent centres for the production of bladed tools like saws, chisels and planes.
Chiyozuru Sadahide II and his apprentice Chiyozuru Naohide, two bladesmiths, work with extraordinary expertise and passion to forge their planes and knives for woodworking. Their kanna (planes) are made by using carbon steel and soft iron backing made from iron elements like ship boilers and late 19th century anchor chains. Each step of the manufacturing process has to be executed with perfect accuracy to achieve the highest quality and sharpest blades. Besides crafting blades for planes, Chiyozuru Naohide challenges traditional techniques to create new works that express the inherent beauty of iron and steel.
Chiyozuru Sadahide II and Naohide talk about the history of their workshop and the challenges of being bladesmiths.
Chiyozuru Sadahide II has been using the forging hammer for decades (top). A glowing blade shortly before it's plunged into cold water for quenching (middle). Chiyozuru Naohide’s knives and matcha spoons are some of collectors’ favourites (bottom)
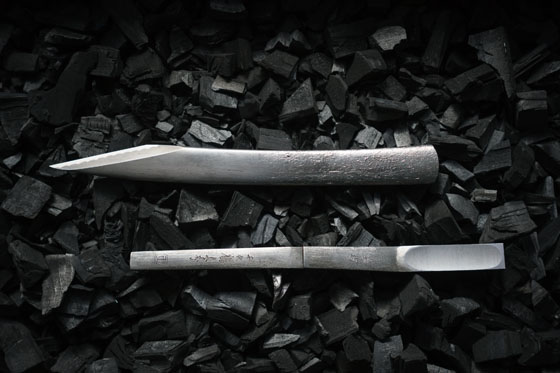
Chiyozuru Sadahide II has been using the forging hammer for decades (top). A glowing blade shortly before it's plunged into cold water for quenching (middle). Chiyozuru Naohide’s knives and matcha spoons are some of collectors’ favourites (bottom)
×Chiyozuru Sadahide II, please tell us a little bit about the history of your workshop.
Two generations ago, my father’s master started the workshop, initially, in Tokyo. One day, at the age of 18, my father went with his friends to a trade fair in Osaka. They encountered a plane from the bladesmith master Chiyozuru Korehide and were utterly captivated. Later, with the age of 20, my father went to Tokyo and asked Chiyozuru Korehide if he could be an apprentice.
But the teacher, at the very beginning, didn’t want to take my father as an apprentice and said, “If you apprentice with me, you’ll live your life in poverty like I have. Give up and go back home to Banshu” (former name of Miki region). After my father insisted, the master accepted his request–one year later. So my father went to the master’s workshop in Tokyo to learn. After two years, he had learned all the most important techniques and returned to Banshu.
He started his own workshop in Miki at the age of twenty-four in the year 1932. It was a very hard time, especially during the war years.
You inherited this workshop from your father, first as his apprentice from the year 1960, then from 1990 under the name Chiyozuru Sadahide II.
When I first officially received the name of Chiyozuru, I was told to three things. The first was to remember how great it is to inherit the name. The second was to be always very respectful to my parents, and the third was to study until death. This work is a life-task.
So maybe in another three years, I will retire from the workshop and leave all this to Morita san, the real family name of my apprentice name (goes by Chiyozuru Naohide, professionally). I totally trust him, and I believe it is worth leaving everything to him because after almost thirteen years of studying and apprenticeship–he will follow in my footsteps.
The workshop in Miki is located in a residential area (top). Interior view of the forging workshop in Ono (bottom)
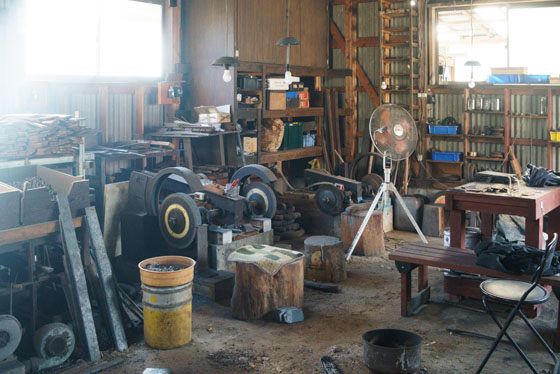
The workshop in Miki is located in a residential area (top). Interior view of the forging workshop in Ono (bottom)
×Chiyozuru Naohide, how did you discover this profession?
Actually, my family has nothing to do with the business of blade smithery. I studied sculpture at university, and my study rooms were located next to the metal class. Sometimes, I had the chance to look at what the people were doing there. Doing some handwork changed something in my life. After I graduated from university, I travelled a lot in Japan and overseas.
At that time I heard of Chiyozuru by chance. That’s why I came to Miki. In the first months, I talked to many local people. By coincidence, they told me Chiyozuru Sadahide’s workshop was in need of an apprentice. That was the very start, when I met my master.
The Japanese concept of passing down craft-related names is unknown to us.
The relationship between a master and his apprentice in Japan is like that of a father and son. It’s often very close. In my case, my family name is Morita. I don’t have to change my real family name. I still use it officially. The name Chiyozuru is used like a business name.
I inherit the business name of my master and will succeed the work he did for his generation. And I will also pass this name to the next generation–to keep this business going on. That’s why I don’t feel I have “thrown away” my own family name. (…)
Why did Miki become such an important centre for blacksmithing?
This area became popular with many bladesmiths and other craftsmen in the late 16th century. There was a famous governor (daimyo, feudal lord) in Japan called Toyotomi Hideyoshi. He campaigned against other Japanese regions, and his resident population had to fight. Therefore, the governor forced a lot of craftsmen, carpenters and technicians to live here. Many craftsmen started as blacksmiths, bladesmiths and toolsmiths because there was a lot to fix. Since then it has become a very popular business. (…)
Chiyozuru Naohide rounds the upper edge of a blade on a large bench grinder (top). The Japanese plane is always pulled while European planes are pushed (bottom)
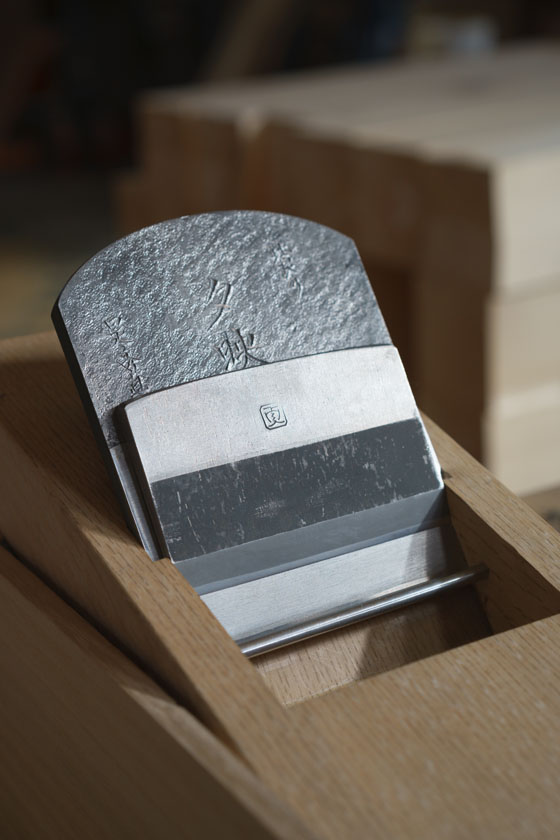
Chiyozuru Naohide rounds the upper edge of a blade on a large bench grinder (top). The Japanese plane is always pulled while European planes are pushed (bottom)
×Naohide, you've written on your website, “Integrating traditional techniques handed down over generations with a modern sensibility is an exciting challenge. It is in the repeated attempts to achieve that new techniques are born.”
Actually less and less people use these bladed tools at home or work. Nowadays, people don’t even sharpen pencils at home. So possibly the only time people use steel tools with blades is when using cooking knives. Less and less people work in the bladesmith business. But that’s the reality now. Politicians have to think about how to keep all these traditional techniques and crafts alive for the future.
First, I think we have get people interested in our field of work.
Second, we should still produce good quality products and hold on to traditional ways–but not in terms of sticking to old things, which never change. New trends and new ideas should be integrated into the traditional craftwork.
Third, people should know our brand name Chiyozuru. We want to make the people who use our products proud. Because being proud of using high quality tools is invaluable.
Each Japanese woodworking plane needs a lever cap (left) and the blade (right). Both are signed with a chisel by hand
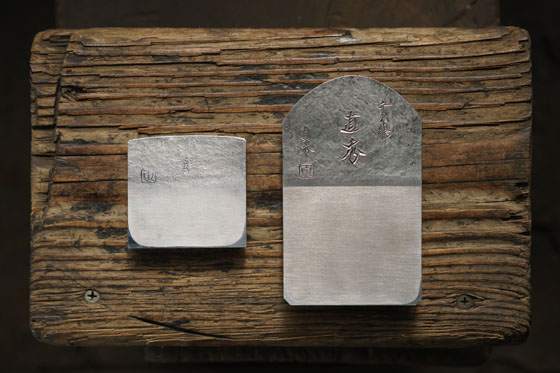
Each Japanese woodworking plane needs a lever cap (left) and the blade (right). Both are signed with a chisel by hand
×This is an excerpt of the interview with Chiyozuru Sadahide II and Chiyozuru Naohide held in January 2017 in Miki, Hyogo.
Photos: Katharina Zettl and Uwe Roettgen
...
About 25portraits
25portraits is a book and documentary project about the inspiring workshops, materials, production processes, products and personalities of 25 craftspeople from all fields of Japanese arts and crafts.