The Futurists: Pedrali
Storia del Marchio di Simon Keane-Cowell
MORNICO AL SERIO (BG), Italia
04.10.17
A long-term investment in the latest production technologies, married with razor-sharp, optimised processes, has helped position Pedrali as a major international player in industrially produced, premium furniture.
Over 5,000 flap-like elements that change colour as the daylight changes make up the facade of Cino Zucchi – CZA Architects’ dynamic skin for Pedrali’s new, state-of-the-art automated warehouse in Bergamo, Italy
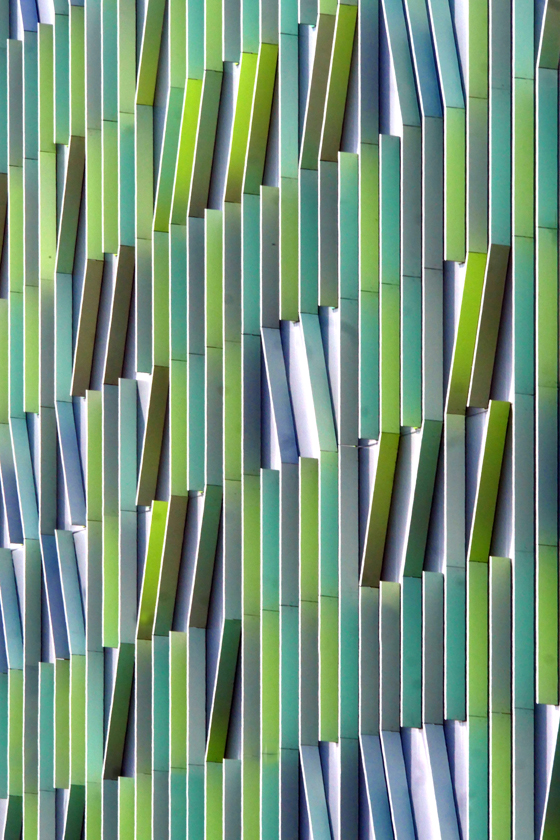
Over 5,000 flap-like elements that change colour as the daylight changes make up the facade of Cino Zucchi – CZA Architects’ dynamic skin for Pedrali’s new, state-of-the-art automated warehouse in Bergamo, Italy
×Monica Pedrali means business.
Having invited me and fellow Architonic colleague from Zurich down to Bergamo for the day to witness at first hand the eponymous Italian furniture brand in action, so to speak, at their high-tech production plant, the company’s ebullient sales and marketing chief – and daughter of founder Mario Pedrali – wastes no time in putting us in the extremely well-drawn picture.
Pedrali teamed up with Italian material-handling experts System Logistics to create the 7,000-square-metre facility, which was planned with the same precision the manufacturer applies to its products
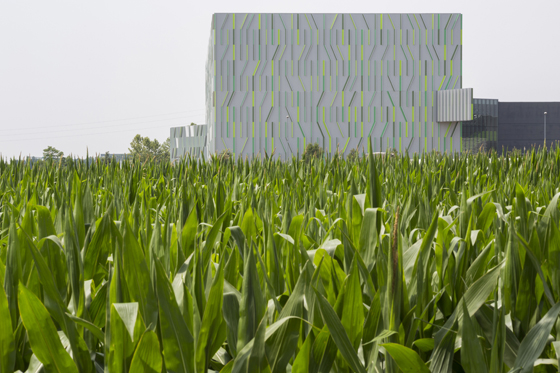
Pedrali teamed up with Italian material-handling experts System Logistics to create the 7,000-square-metre facility, which was planned with the same precision the manufacturer applies to its products
דPedrali is situated in very rich territory,” she explains. “On the one hand, we draw on this part of Lombardy’s traditional know-how in industrial production – formerly textiles, now steel production and injected plastic for the car industry and for furniture components. On the other, we are influenced by nearby Milan as a creative hub, with its iconic design practice, the polytechnic, the Triennale, the Salone and so on. It’s this context, and our commitment from the start, when my father founded the business in 1963, to investing in the latest technology – to save energy, optimise performance and make us more competitive – that has allowed us to grow. We now have 250 employees and opened a dedicated wood-production factory in Manzano, Udine, ten years ago, which we recently expanded.”
Pedrali’s new logistics building can house over 17,000 pallets, with five robots operating around the clock, storing and retrieving both finished products and semi-finished components across a cathedral-like volume, 135m in length and 29m in height
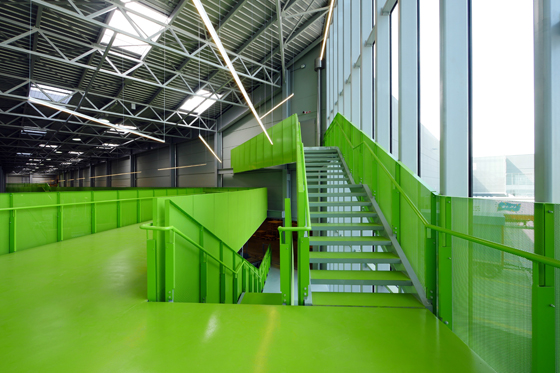
Pedrali’s new logistics building can house over 17,000 pallets, with five robots operating around the clock, storing and retrieving both finished products and semi-finished components across a cathedral-like volume, 135m in length and 29m in height
×The word loquacious springs to mind, as I’m busily taking notes. (“People say I talk too much,” Monica laughs.) But what you very quickly realise is that this is anything but rehearsed sales and marketing speak. It’s passion and authenticity talking. And let’s be honest: if you were part of the success story that is Pedrali, you’d have a lot to say about it, too. Beyond the company’s discerning collaborations with designers (both established names and emerging design talent) who understand how to truly exploit the manufacturer’s expertise in industrial production, beyond their highly photogenic fair stands, there’s a design business that’s consciously designed its business to be as innovative, well-crafted and sustainable as its products.
A long-term investment in robotic production at Pedrali dovetails with its commitment to the development of proprietary manufacturing technologies and as much control of the supply chain as possible
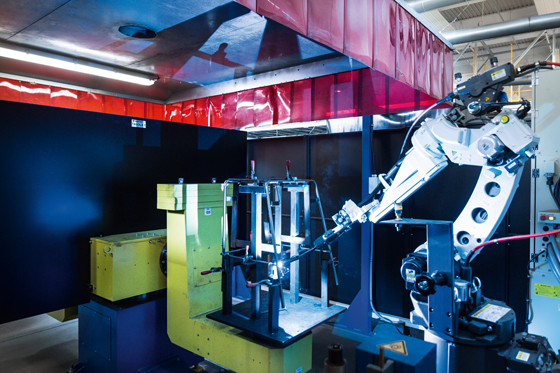
A long-term investment in robotic production at Pedrali dovetails with its commitment to the development of proprietary manufacturing technologies and as much control of the supply chain as possible
×Their brand “Made in Pedrali” strapline cleverly says it all. While a piece of hat-tipping, of course, to the heritage and cultural value of Italian-made design, it also foregrounds the fact that Pedrali has never outsourced any aspect of its production. Indeed, it has evolved over time to control as much of the supply chain as possible, buying the materials it requires several years in advance and tirelessly translating its R&D department’s innovative thinking into proprietary production technologies. It makes no secret of the fact that it has invested heavily in fully automated machinery, state-of-the art robots that operate 24 hours a day on the factory floor, delivering even higher levels of quality and precision (and, of course, efficiency). “20 years ago, we had 70 people working on welding,” explains Monica. “Now we have just nine. Our team is involved much more now in real added-value work. Monitoring, finishing, checking.”
"Made in Pedrali" is no empty marketing slogan. The manufacturer has only ever produced in-house, with automated production lines and its team of highly skilled workers creating a collection that boasts over 85,000 different forms
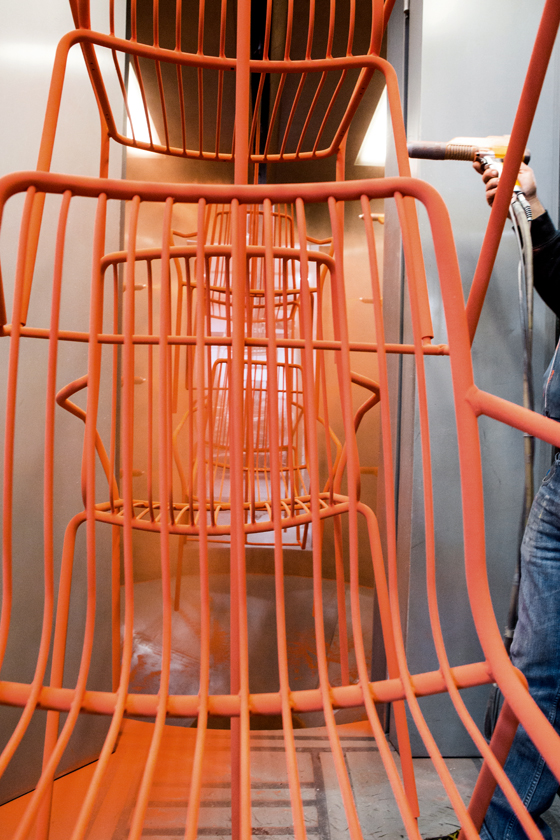
"Made in Pedrali" is no empty marketing slogan. The manufacturer has only ever produced in-house, with automated production lines and its team of highly skilled workers creating a collection that boasts over 85,000 different forms
×And there’s a lot to check. Pedrali has successfully secured its position as one of the go-to design manufacturers for architects looking for expressively designed, contemporary furniture that they can rely on – not only in terms of quality and longevity, but also in terms of delivery. Aside from the fact that it is able to hold thousands of pieces in stock, the company can, thanks to its optimised processes, fulfil even the largest of contract orders within a few weeks. With its complete collection featuring a staggering 85,000 different forms, which can then be specified with a range of colours, upholstery and finishes, Pedrali’s technology-first, streamlined MO means creatively uncompromised solutions for clients, implemented within those critical project deadlines.
The opening of a dedicated wood-production facility in Manzano, Udine, ten years ago has helped Pedrali position as a leader in industrially produced furniture across a range of materials
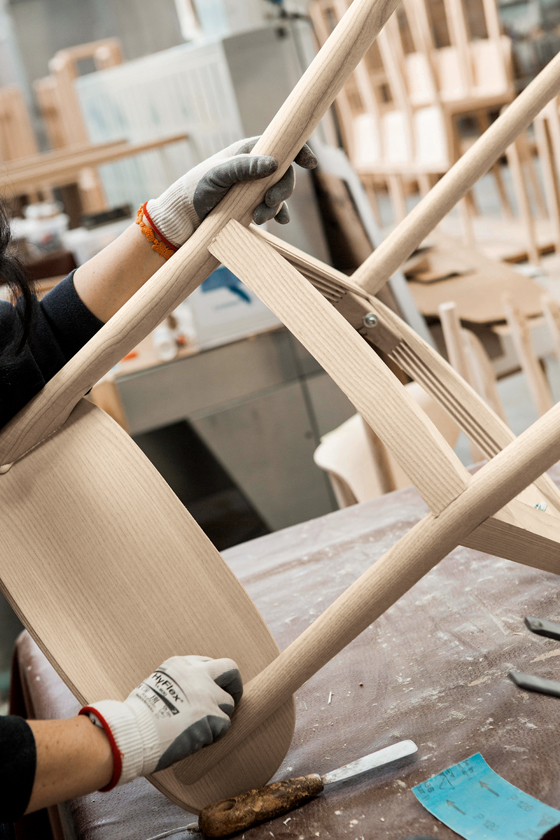
The opening of a dedicated wood-production facility in Manzano, Udine, ten years ago has helped Pedrali position as a leader in industrially produced furniture across a range of materials
×Moving through Pedrali’s Bergamo factory with Monica and her team is, even for this seasoned design editor, an eye-opener. Laser-cutting, bending, welding, powder-coating, as well as plastic injection-moulding, for the most part automated to a high degree via a cohort of super-agile robots and smart machinery (the company invests at least €10 million a year in new technology), makes for an industrial landscape characterised by high productivity and low-to-no waste. Moulds weighing several tonnes and costing up to an eye-watering €600,000 are craned in and out of position. Oh, and it’s hot.
Pedrali’s products add value and richness to the materials they employ. Wood, for example, is used with low consumption and features water-based finishes. Plastic reads like leather. From top to bottom: Nym, Buddy and Fox collections
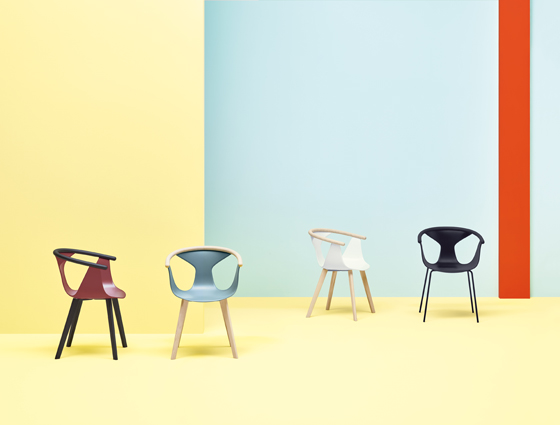
Pedrali’s products add value and richness to the materials they employ. Wood, for example, is used with low consumption and features water-based finishes. Plastic reads like leather. From top to bottom: Nym, Buddy and Fox collections
×Trundling at regular intervals overhead through several of the factory buildings is a new skytrain, which connects manufacturing areas with Pedrali’s new architectural-landmark logistics facility. The building’s optically textural facade – designed by Milan-based Cino Zucchi Architects and which features over 5,000 flap-like elements in different hues of green that change colour as the daylight changes – is as dynamic as what goes on inside. Planned by Pedrali’s in-house team in collaboration with Italian material-handling experts System Logistics, the 85,000-square-metre, fully automated warehouse, with its remarkable scale, low-lighting levels and hushed air, is a veritable cathedral of industry. With room for over 17,000 pallets, the space is home to five robots that operate around the clock, storing and retrieving in a perfect choreography both finished products and semi-finished components across a vast volume measuring 135 metres in length and 29 metres in height.
Pedrali’s capacity to hold thousands of pieces in stock, married with its optimised processes, means it can fulfil even the largest of contract orders within a few weeks, making it one of the go-to producers for architects
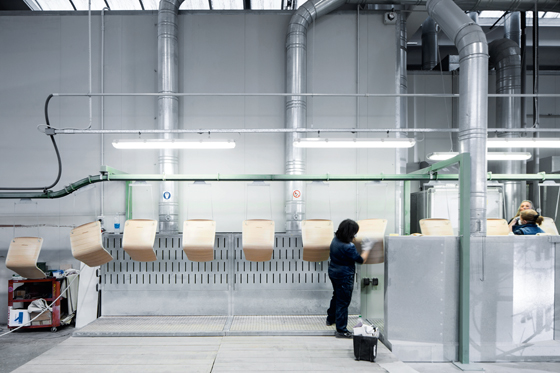
Pedrali’s capacity to hold thousands of pieces in stock, married with its optimised processes, means it can fulfil even the largest of contract orders within a few weeks, making it one of the go-to producers for architects
×In essence, the new facility is as much a piece of product design as it is a piece of architecture. Conceived of from the inside out, this is high-tech product engineering – a machine – which is then skinned with an architecturally expressive envelope. It also functions as a metaphor for Pedrali’s essential approach to design: always impeccably planned, fit-for-purpose, but with a strong aesthetic value. Design excellence in short.
Pedrali invests an average of €10 million a year in new technology, making for a high-productivity, low-to-no-waste industrial landscape
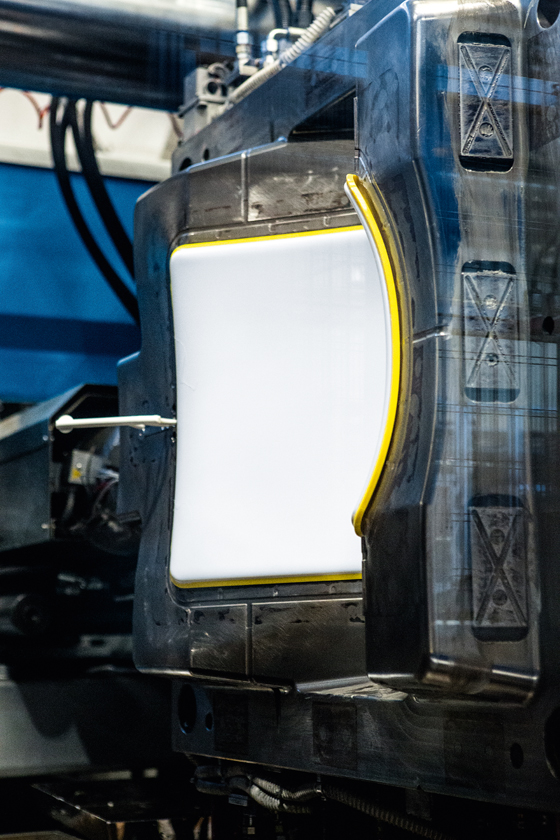
Pedrali invests an average of €10 million a year in new technology, making for a high-productivity, low-to-no-waste industrial landscape
×This rigour is also applied to how the company works, however, not just what it makes. Pedrali has been committed for a number of years now to leading the way in its sector when it comes to best-practice in environmental and social responsibility. In addition to using only 100% water-based finishes for its furniture – among the first chair manufacturers in Italy to do so – as well as installing LED lighting throughout its offices and production plants, Pedrali is fully ISO-14001-certified. This means it operates a proven environmental-management system across the board. All production processes are certified. Every department is expected to present a budget annually to reduced energy usage. “It has been a major investment for us,” explains Monica, “but we are convinced that this is good for business – for all businesses. Adhering to these standards is not just a cosmetic exercise. It’s a key part of our sustainability strategy.”
Pedrali sales and marketing chief Monica Pedrali: "Our commitment, from when my father founded the business in 1963, to invest in the latest technology – to save energy, optimise performance and make us more competitive – has allowed us to grow"
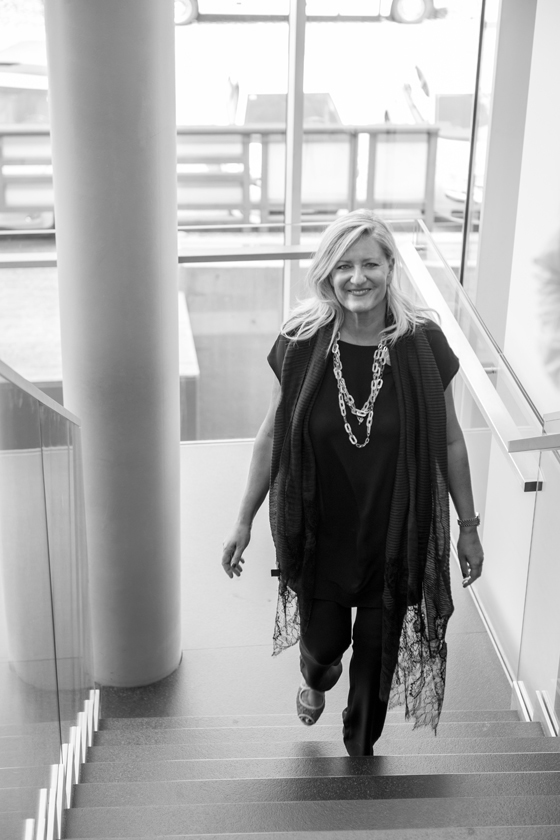
Pedrali sales and marketing chief Monica Pedrali: "Our commitment, from when my father founded the business in 1963, to invest in the latest technology – to save energy, optimise performance and make us more competitive – has allowed us to grow"
×The fortified old town of Bergamo has just been recognised by UNESCO as a World Heritage Site. Pedrali may be somewhat its junior in chronological terms, but it is proving it’s committed to the long-haul, with a smart, creative and agile business that’s fit for future challenges.
© Architonic