Precision Casting from the Witch’s Kitchen
Texte par Nora Schmidt
Berlin, Allemagne
01.04.11
When designers and leading industrial enterprises put their heads together, it usually gets exciting. While such a collaboration allows industry the possibility of demonstrating its special capabilities in a completely new context, its manufacturing processes, conversely, provide an unexpected treasure trove of new design solutions for creative minds. This is what happened in the collaboration between SCHMOLZ + BICKENBACH Guss Gruppe and the Berlin-based design studio Formfjord.
'Cioccolato' made from cast stainless steel, designed by Formfjord in collaboration with SCHMOLZ+BICKENBACH, photo by Jan Hosan for pure cast
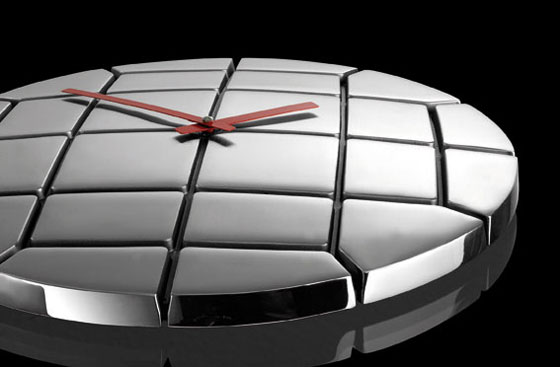
'Cioccolato' made from cast stainless steel, designed by Formfjord in collaboration with SCHMOLZ+BICKENBACH, photo by Jan Hosan for pure cast
×When designers and leading industrial enterprises put their heads together, it usually gets exciting. While such a collaboration allows industry the possibility of demonstrating its special capabilities in a completely new context, its manufacturing processes, conversely, provide an unexpected treasure trove of new design solutions for creative minds. This is what happened in the collaboration between SCHMOLZ + BICKENBACH Guss Gruppe and the Berlin-based design studio Formfjord.
'Cioccolato' is the first object of the new design label pure cast, photo by Jan Hosan for pure cast
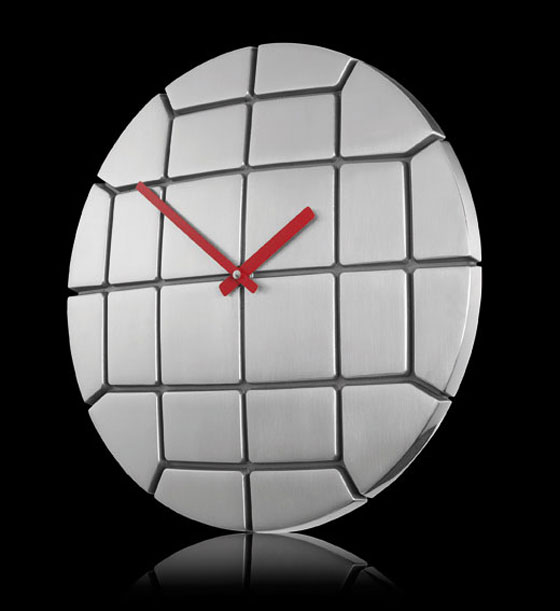
'Cioccolato' is the first object of the new design label pure cast, photo by Jan Hosan for pure cast
×The core competence of the European market leader for cast stainless-steel products lies in particularly demanding casting solutions: 'Just tell us how you want the product to look. We’ll make sure that such an artistic casting can be produced.' The company has already produced complicated castings for such prominent artists as Jeff Koons and Anish Kapoor, proving that Andreas Höller, director of the SCHMOLZ + BICKENBACH foundry in Ennepetal, is not exaggerating. Together with Formfjord, SCHMOLZ + BICKENBACH now wants to prove these outstanding capabilities in another field, namely product design.
The first product to emerge from this new collaboration is the 'Cioccolato' wall clock, which is produced as a limited edition of 1,000 units. It marks the beginning of a new design collection of premium-cast stainless-steel products, launched under the label pure cast
During this year’s Salone del Mobile, 'Cioccolato', together with working models and off-casts, will be showcased at the 'Poetry Happens' exhibition in Lambrate.
Challenge the limits of casting technology: 'Cioccolato by Formfjord, photo by Jan Hosan für pure cast
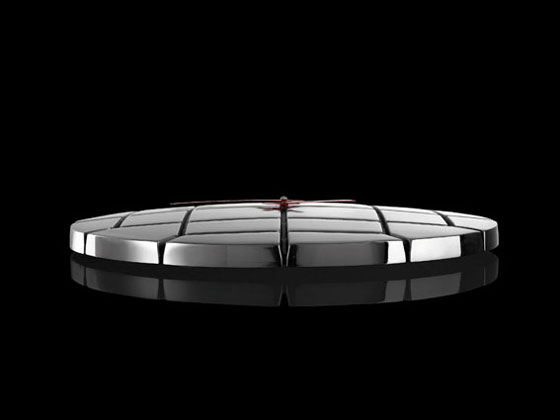
Challenge the limits of casting technology: 'Cioccolato by Formfjord, photo by Jan Hosan für pure cast
×Architonic met the designers Fabian Baumann and Sönke Hoof from Formfjord at their studio in Berlin to discuss this exciting work process.
How did this unusual collaboration come about?
Fabian Baumann: The approach was a surprise to us because, up to that point, we didn‘t even know who SCHMOLZ + BICKENBACH were. But we have been hooked on the project since our first factory tour. SCHMOLZ + BICKENBACH already has quite some experience in the field of artistic castings. The collaboration with designers, therefore, was actually not that far-fetched.
Sönke Hoof: An excellent idea because the specialty of the foundry, namely the precision casting of stainless steel, has barely been used in the field of design up to this point. Just imagine that castings of the highest quality are produced daily at SCHMOLZ + BICKENBACH and then simply disappear into large machines – what a pity.
You are a pretty young design studio. Why do you think your studio was chosen?
FB: One aspect certainly was our previous work. I believe another decisive reason for collaborating with us was that we are a team consisting of a product designer and a mechanical engineer, and therefore already bring along considerable technical know-how.
The wax form is examined carefully. It is deburred by hand and given a serial number, photo by Jan Hosan for pure cast
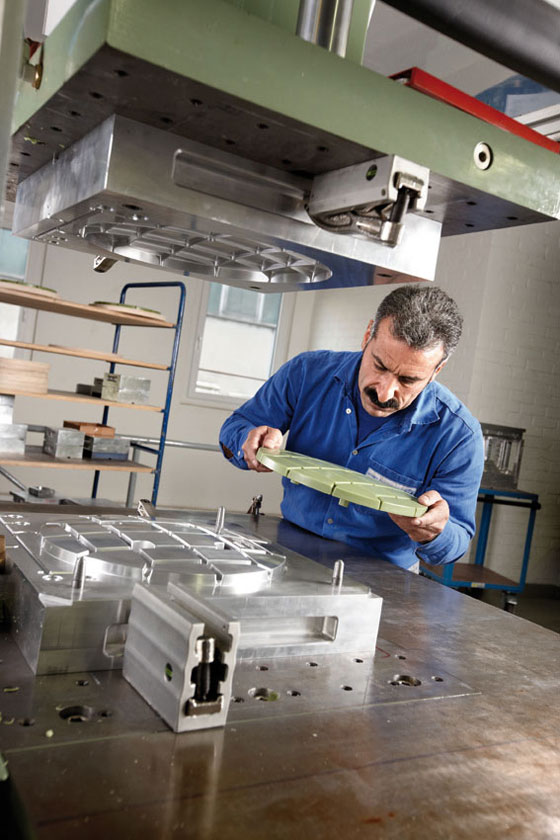
The wax form is examined carefully. It is deburred by hand and given a serial number, photo by Jan Hosan for pure cast
×What was the brief that SCHMOLZ + BICKENBACH presented you with?
SH: We were to design a wall clock, in other words an object that is sculptural but also has a clear function. The wall clock was to be made of stainless steel in a precision-casting process – other than that, there were no additional requirements.
FB: We were specifically asked to challenge the limits of casting technology with our design. We were to design a product that demonstrates the capabilities of a foundry in the form of a sample of sorts. This is the reason why we were initially invited to the factory in order to familiarise ourselves with the process. That was an overwhelming experience. Different alloys are prepared at the factory for various requirements, like in a witch's kitchen.
SH: Although SCHMOLZ + BICKENBACH repeatedly pointed out, 'You just worry about the design and we'll take care of the casting', it was very important to us to design a product that can be immediately recognised as a casting. The point, therefore, was to utilise the formal capabilities of the process very purposefully, while still preserving the clear language of forms that is typical of our work.
How exactly does this process work?
FB: In precision stainless-steel casting, a wax pattern that geometrically corresponds to the clock, at full scale, is initially cast in an aluminium tool. This wax pattern is then encased with several ceramic layers. After the wax melts out of the ceramic mold, the mold is fired, giving it the stability to withstand the casting pressure. It is then filled with the molten stainless steel, while it is still in the hot state.
Does that mean that the wax form and mould are lost in the process?
FB: Exactly. The ceramic mold has to be smashed after the stainless steel has cooled down.
SH: But this also means that there is no seam – that's the ingenious aspect of the process. And all these processes are attended to with complex manual labour. Small joints are filled and inaccuracies are corrected. The employees in Ennepetal really know every trick.
Alternate dipping in liquid ceramics and sanding with fire-resistant substances produce a ceramic coating around the wax forms. After the wax has melted, the ceramic form is fired at 1,000 degrees Celsius / Fabian Baumann and Sönke Hoof of Formfjord
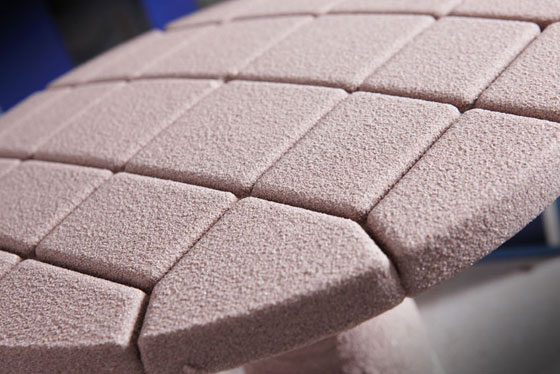
Alternate dipping in liquid ceramics and sanding with fire-resistant substances produce a ceramic coating around the wax forms. After the wax has melted, the ceramic form is fired at 1,000 degrees Celsius / Fabian Baumann and Sönke Hoof of Formfjord
×If 'everything is possible', to what extent were you able to challenge the limits of the process?
FB: Naturally, not everything is possible – but quite a lot. In any case, we wanted to resist the temptation to produce arbitrary, free-form designs. Rather, we examined the technical characteristics of the process, with which we subsequently worked in detail.
SH: With 'Cioccolato', you can see this in different places. For example, the pronounced grooves.
FB: We developed a special drawing of the clock, dividing the dial into 12 sections. The deep grooves provide the clock with a certain mass and make it possible to play with the drafts that are characteristic for castings. Their highly pronounced appearance initially resulted from the necessity to create space for the waste heat during casting as the groove depth increased.
SH: But the slanted walls are only one of many geometric intricacies. For example, the surface of the clock is curved to a different degree than the bases of the grooves. Consequently, their depth and, therefore also, their width varies. The slight curvature of the grooves boosts the dynamics of the design.
FB: The result is a truly complex body, on which each individual surface is curved several times. The complicated aspect with regard to the casting process is that the molten steel constantly needs to flow 'around the corner'. Considering the small wall thickness that is sometimes less than 2 mm, it is truly an art to manage to fill the mold uniformly.
When the correct casting temperature is reached, the oven is tilted and the molten high-grade steel is poured, bubbling into a "pan", which, in turn, is moved by a crane to the individual moulds, photo by Jan Hosan for pure cast
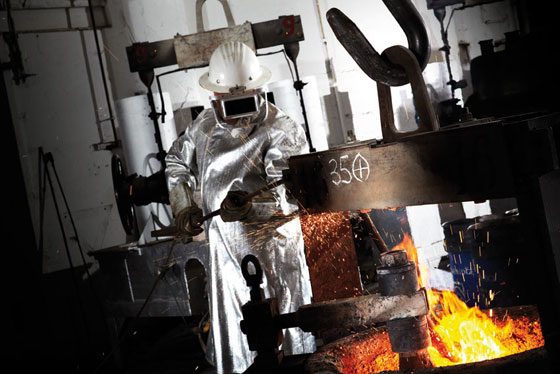
When the correct casting temperature is reached, the oven is tilted and the molten high-grade steel is poured, bubbling into a "pan", which, in turn, is moved by a crane to the individual moulds, photo by Jan Hosan for pure cast
×The molten steel is poured, on command, into the moulds and acquires its predetermined form, photo by Jan Hosan for pure cast
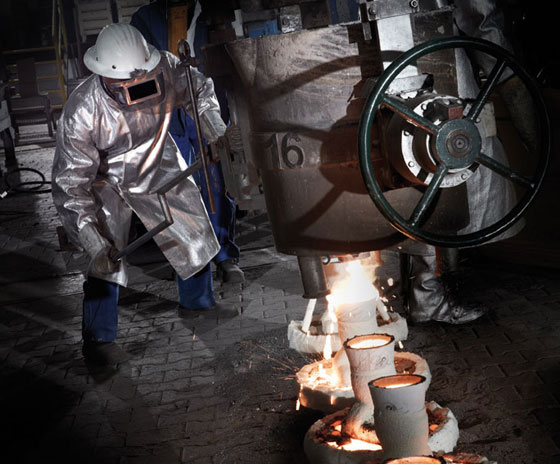
The molten steel is poured, on command, into the moulds and acquires its predetermined form, photo by Jan Hosan for pure cast
×While the freshly cast clocks still glow red in their moulds, the next batch is being thought about, photo by Jan Hosan for pure cast
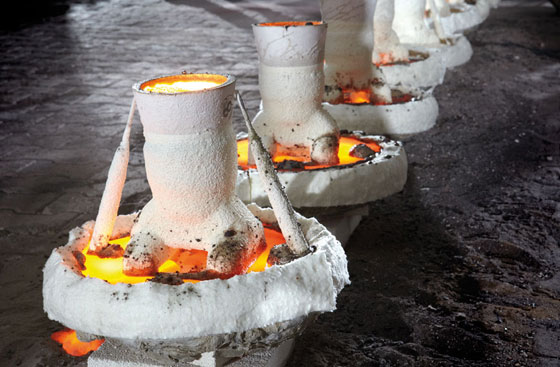
While the freshly cast clocks still glow red in their moulds, the next batch is being thought about, photo by Jan Hosan for pure cast
×How is the collaboration with the foundry working out? After all, two worlds are colliding here: mechanical engineering and design.
SH: It was very motivating to see that no effort was spared in order to realise our designs. We hardly had to make any compromises and, when we did, the reasons for the objections were always related to the production technology and, therefore, always appeared plausible to us.
FB: In fact, we always have a functional or constructive reason for aesthetic decisions. With 'Cioccolato', we focused on certain functional and technical details of the casting process from the beginning. It was important to us to create a clear shape despite the freedom that the process offers; the complexity is only apparent at second glance.The collaboration was extremely fruitful and professional from our first visit to the foundry onwards. Once it became clear that we agreed on the decisive issues after the presentation of the first designs, mutual trust grew naturally.
What are your future plans in this respect?
SH: We are actually already working on a few other projects. We are curious to see what else evolves out of our collaboration.
Thank you for talking to us.
On cooling, the ceramic shells break open and the newly cast unique pieces become visible for the first time, photo by Jan Hosan for pure cast
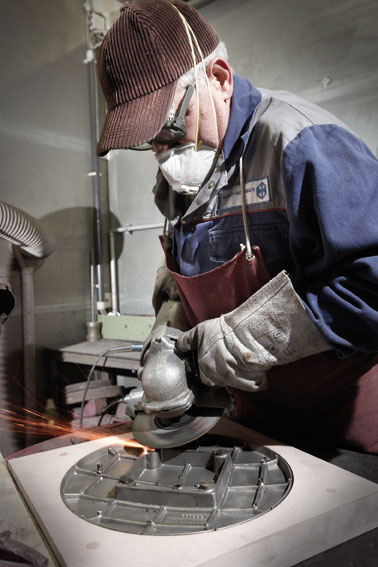
On cooling, the ceramic shells break open and the newly cast unique pieces become visible for the first time, photo by Jan Hosan for pure cast
×The perfect '19/11' alloy for casting 'Cioccolato' is prepared with precision according to a recipe. Chrome, silicon, molybdenum and iron are all added to the mix, photo by Jan Hosan for pure cast
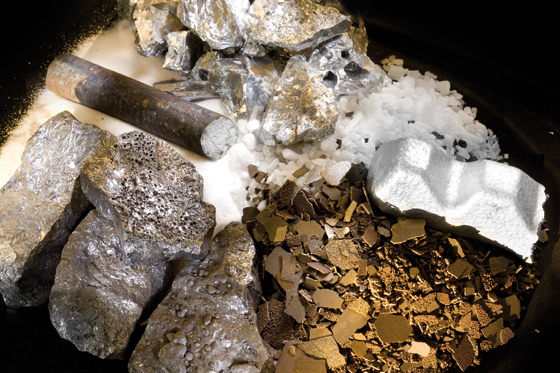
The perfect '19/11' alloy for casting 'Cioccolato' is prepared with precision according to a recipe. Chrome, silicon, molybdenum and iron are all added to the mix, photo by Jan Hosan for pure cast
×