So Transparent: London's iconic Crystal Palace reloaded – Part I
Texto por selected by Materials Council
Reino Unido
19.05.14
One of most iconic architectural structures of the 19th century – London’s legendary Crystal Palace – is being reborn, with a host of international starchitects in the running to rethink it. Leading materials consultancy MATERIALS COUNCIL investigates the exciting possibilities this landmark project offers in terms both of material innovation and of cutting-edge building technologies.
Illustrative visualisation of the new Crystal Palace masterplan, on its original South London site. Images © ZhongRong Group
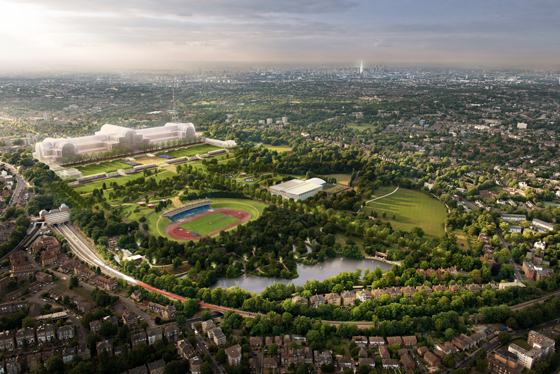
Illustrative visualisation of the new Crystal Palace masterplan, on its original South London site. Images © ZhongRong Group
×Last October Chinese developer ZhongRong Group announced their intention to rebuild the iconic Crystal Palace, originally built for Britain’s 1851 Great Exhibition – an international expo of industry and culture from the country’s vast empire and beyond. Initially billed as a faithful reconstruction of the original structure, the group, in the face of criticism from both the public and the architectural community, later tendered a competition to create a 'spiritual successor'.
Materials Council decided to explore, in advance of the winner being announced, how the requirements specified by the original design committee, the original building’s design innovations, and contemporary glazing and material technologies could inform a modern-day interpretation of the Crystal Palace.
....
Illustrative visualisations of the new Crystal Palace – view of the terrace (top) and an interior view (above). Images © ZhongRong Group
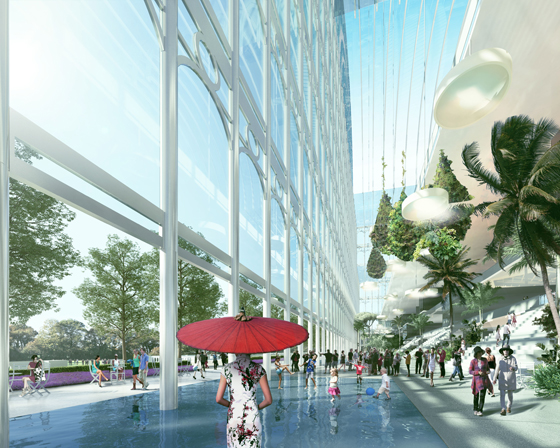
Illustrative visualisations of the new Crystal Palace – view of the terrace (top) and an interior view (above). Images © ZhongRong Group
×The original Crystal Palace, erected in Hyde Park, London, was a radical architectural advancement. It was designed by Joseph Paxton after an unsuccessful competition to find a suitable design satisfying the building committee's key specifications. They stipulated that the building be:
• temporary
• simple
• as cheap as possible
• economical to build in less than a year before the already scheduled exhibition
It has been regarded as marking the start of architectural modernity, trumpeted by Le Corbusier as the ‘herald of a new age’, and is arguably the progenitor of the ‘High Tech’ architecture of Norman Foster, Richard Rogers, et al.
The Crystal Palace was a paradigm shift. Not only in what an architectural space could be but also the design concepts, engineering and construction processes required to successfully realise a building of an entirely new materiality and subject to unprecedented constraints.
The Crystal Palace was dismantled and rebuilt at its eventual home in Sydenham Hill
Design schematic of the main transept and repeating cast-iron shell
Interior photograph showing the modular cast-iron structure
After its initial six-month life in Hyde Park, the original Crystal Palace was dismantled and relocated to its eventual home in Sydenham Hill, South London. Here, an expanded design of the Crystal Palace was rebuilt using most of the original components as the basis of a larger, but quite different in form, incarnation, which stood for 82 years before succumbing to fire. It is this location, which, in the interim, has lent its name to the surrounding neighbourhood, that the Zhong Rong Group controversially intends to redevelop.
To protect the development of the site a 1990 Act of Parliament, rather vaguely, insists that any building placed there should ‘contain a predominance of glass and metal or similar materials and that the building should reflect the spirit of the original Crystal Palace’. Paxton's pioneering design concepts and construction principles are illustrated in the competition brief as the key aspect of this 'spirit'.
Zaha Hadid & Anish Kapoor, Grimshaw, Haworth Tompkins, Marks Barfield, David Chipperfield and Rogers Stirk Harbour & Partners make up the shortlist of architects announced at the end of February. Up to three teams from the shortlist will be invited to submit initial design concepts with the winner eventually being announced in the summer.
Construction of the prefabricated structural elements
The breathtaking fountains at Crystal Palace park were fed by 2 water towers built by Isambard Kingdom Brunel
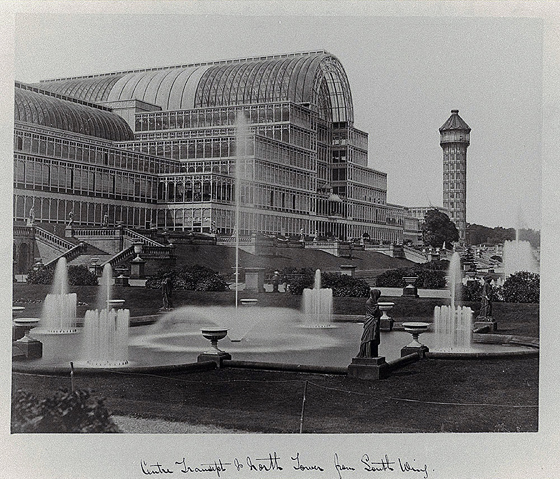
The breathtaking fountains at Crystal Palace park were fed by 2 water towers built by Isambard Kingdom Brunel
×Modular, prefabricated system
Paxton expanded upon previous experimentations in the construction of glasshouses to propose a design that surpassed the building committee's specifications. It was vastly cheaper and quicker to construct than any other proposal or form of building of comparable size, going from sketch to completed building in less than nine months.
Based around the dimensions of the largest available glass sheet, Paxton created an incredibly flexible, modular, gridded design that could form a variety of spaces. It even allowed him to alter the design during the course of the construction.
The structure comprised repeating modules made from a system of prefabricated cast-iron elements, exploiting for the first time the benefits of prefab construction. These cast-iron parts were incredibly easy, fast and economical to manufacture on a large scale. Produced under controlled conditions, accuracy and quality was ensured.
Leadenhall building's steel mega-frame during construction
Construction was also exceedingly quick. The building could be assembled section-by-section as parts arrived on site, with some sections standing within 18 hours of leaving the factory. This enabled the majority of the building to be completed in just five months.
While the use of prefabricated steel members and other components are now commonplace, processes are still being refined to maximise the benefits afforded. The construction of Rogers Stirk + Harbour's Leadenhall building breaks new ground in this regard.
The high-profile location, tight footprint and narrow streets of the site present considerable challenges to construction. As a result 85% of the building's built value consists of prefabricated and off-site manufactured elements. Instead of using a central concrete core the structure is primarily provided by a steel perimeter mega-frame. The services tower of the building comprises prefabricated structural steel 'tables' preassembled off-site with mechanical and electrical plant and precast concrete slabs.
The mega-frame provides the building's structure without a central concrete core
Glazing Leadenhall's envelope (left), and the bright yellow, prefabricated, stacked 'tables' of Leadenhall's services tower
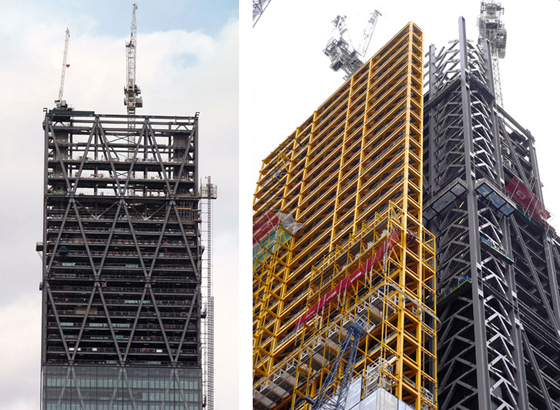
Glazing Leadenhall's envelope (left), and the bright yellow, prefabricated, stacked 'tables' of Leadenhall's services tower
×The project has also pioneered the use of radio frequency identification (RFID) software to track building components through manufacture, delivery and installation. In conjunction with BIM the contractors have refined the just-in-time assembly process, enabling them to anticipate delays downstream and take preventative action.
This has enabled construction to minimise disruption for neighbours, reduce noise, increase on-site safety, speed up erection and reduce the required on-site workforce by around 40% compared to traditional builds.
The Broad Group of China believe their 95% prefabricated modular technology will allow them to create the world's tallest building in only 9 months, including just three months onsite. Construction will reportedly be one tenth the cost of the current tallest building, the Burj Khalifa.
Visualisation of the world's tallest building as planned by Broad Group. The group claim the building will only require three months on-site construction. Image courtesy of Broad Group
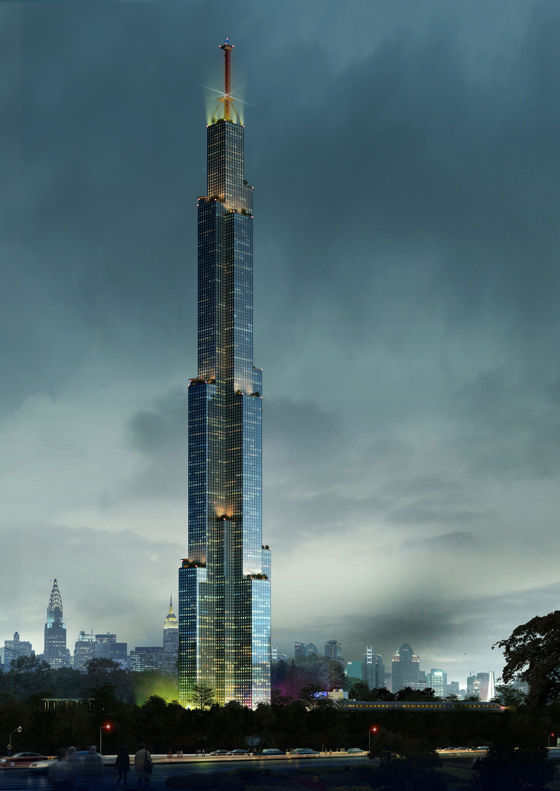
Visualisation of the world's tallest building as planned by Broad Group. The group claim the building will only require three months on-site construction. Image courtesy of Broad Group
×The boundaries of glass
The Crystal Palace was, at the time, the largest glazed building in the world. Today many of our largest buildings are covered in a glazed skin but few push the envelope of what is now possible at the extreme end of glass manufacturing and technology.
Paxton based his Crystal Palace design around the dimensions of the largest available standard sheet of glass. At the time a pane of 0.2 x 1.2 metres, produced using the recently invented cast glass plate manufacturing process. This meant the facade could be glazed astonishingly quickly. Using the standard panes without trimming, a team of 80 glaziers installed them at a rate of 18,000 panes per week.
Today the largest sheets of float glass offered by manufacturers measure 3.3 metres wide as standard and at most 18 metres long, though some manufacturers can produce mega sheets at 4 metres wide. Their dimensions are dictated by the existing machinery used in their manufacture and the logistics involved. Yet rarely, if ever, will you see glass of this scale employed across the facade of a building. Their cost and the sheer practicalities of transporting and installing such sheets being wildly prohibitive.
The refined 'Apple Cube' Mark 2 (top) enveloped in just 15 sheets of mega-glass. Image courtesy of Eckersley O'Callaghan. The 5th Avenue 'Apple Cube' Mark 1 (above) had 18 sheets of glass per face. Image by Ed Uthman
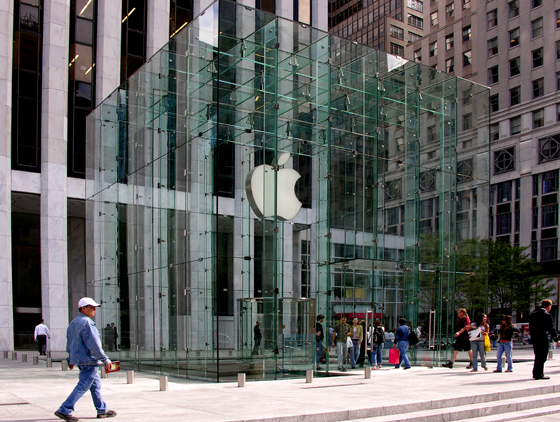
The refined 'Apple Cube' Mark 2 (top) enveloped in just 15 sheets of mega-glass. Image courtesy of Eckersley O'Callaghan. The 5th Avenue 'Apple Cube' Mark 1 (above) had 18 sheets of glass per face. Image by Ed Uthman
×However, there are examples of smaller structures that have utilised mega sheets of glass that hint at what an interpretation of Crystal Palace free of these constraints could look like.
In their designs for Apple stores around the world, the partnership of specialist glass fabricators Seele Sedak and facade and glass engineers Eckersley O'Callaghan has pushed the boundaries of what is possible with glass production and construction at the extreme end of the spectrum. And in Apple they have a more than willing patron and instigator.
The redesign of the iconic glass cube entrance to the 5th Avenue Apple Store in New York reduced the number of glass sheets per face down from 18 to just three panes of five-ply, ionoplast-laminated safety glass measuring 10.3 x 3.3 metres. Held together by titanium fixings, fitted into the glass panels during the lamination process making them almost completely concealed, the structure is virtually entirely glass.
Apple’s determination to use, at 13 metres, the world's largest curved glass sheets for the entrance to their Shanghai store even propelled them to develop a new production facility with their local Chinese glass fabricators that could match their exacting demands. Curved panels of a similar scale are expected to be used on an unprecedented scale at the new Apple campus in Cupertino, designed by Foster + Partners architects, glazing the entire facade.
'Apple Campus' by Foster + Partners proposes to use the world's largest sheets of curved glass
An interesting development in architectural glass is the new availability of Corning's Gorilla Glass; ubiquitous in the screen technology of almost every electronic device we prod throughout the day.
Corning's unique 'fusion-draw' glass-manufacturing process and chemical-strengthening techniques produce an incredibly strong, thin, damage-resistant yet flexible glass with excellent surface quality and optical clarity. Its greater strength allows it to be used in architectural applications in much smaller thicknesses but with the same strength and stiffness. However, its current cost again limits its implementation.
Unfortunately, Corning's exploration of architectural applications has so far not gone much further than turning every surface into a touch screen. Envisioning an unpleasantly greasy future of universally smudged and streaked interiors. So while extreme structural glass designs are possible they're unfortunately not reasonably practical.
The slumped glass 'X's of REX's Vakko Fashion Centre make it appear as if wrapped in plastic. Images by Iwan Baan, courtesy of REX
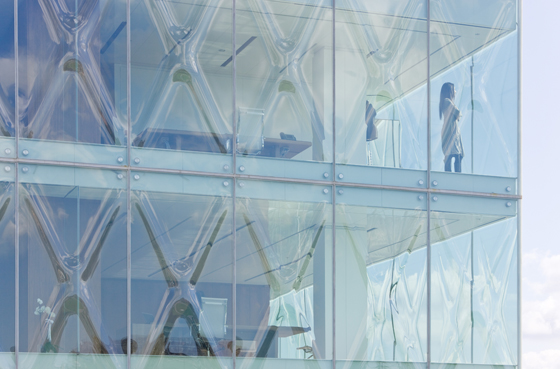
The slumped glass 'X's of REX's Vakko Fashion Centre make it appear as if wrapped in plastic. Images by Iwan Baan, courtesy of REX
×Another issue with using glass in this manner is thermal performance, due to its poor insulation and issues of solar control. To use insulated glazed units (IGU) or highly reflective solar coatings would defeat the aesthetic purity these minimal, transparent glass structures are designed to achieve in the first place.
Perhaps REX's approach to the glazing of the Vakko Fashion Center in Istanbul offers a compromise of structural performance, insulation performance and visual clarity. By using a slumping glass manufacturing process the architects formed an X into one glass face of an IGU. The result was a much stronger and stiffer IGU, eliminating the need for additional structural columns around the perimeter of the building.
_
_